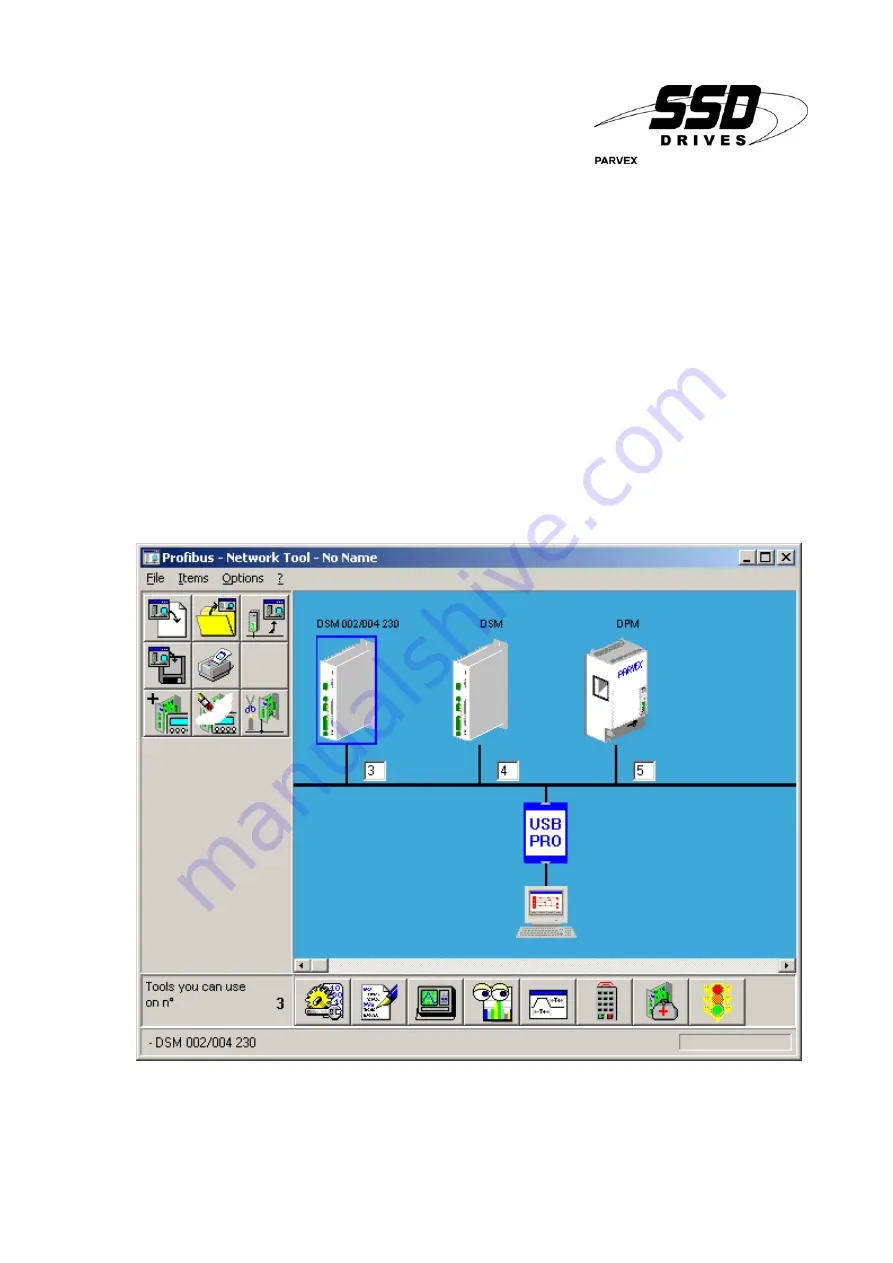
SSD Parvex SAS
8, avenue du Lac - B.P. 249
F-21007 Dijon Cedex
www.SSDdrives.com
DIGIVEX Motion
PROFIBUS
User and commissioning manual
PVD 3554 GB – 01/2004
SSD Parvex SAS
8, avenue du Lac - B.P. 249
F-21007 Dijon Cedex
www.SSDdrives.com
DIGIVEX Motion
PROFIBUS
User and commissioning manual
PVD 3554 GB – 01/2004