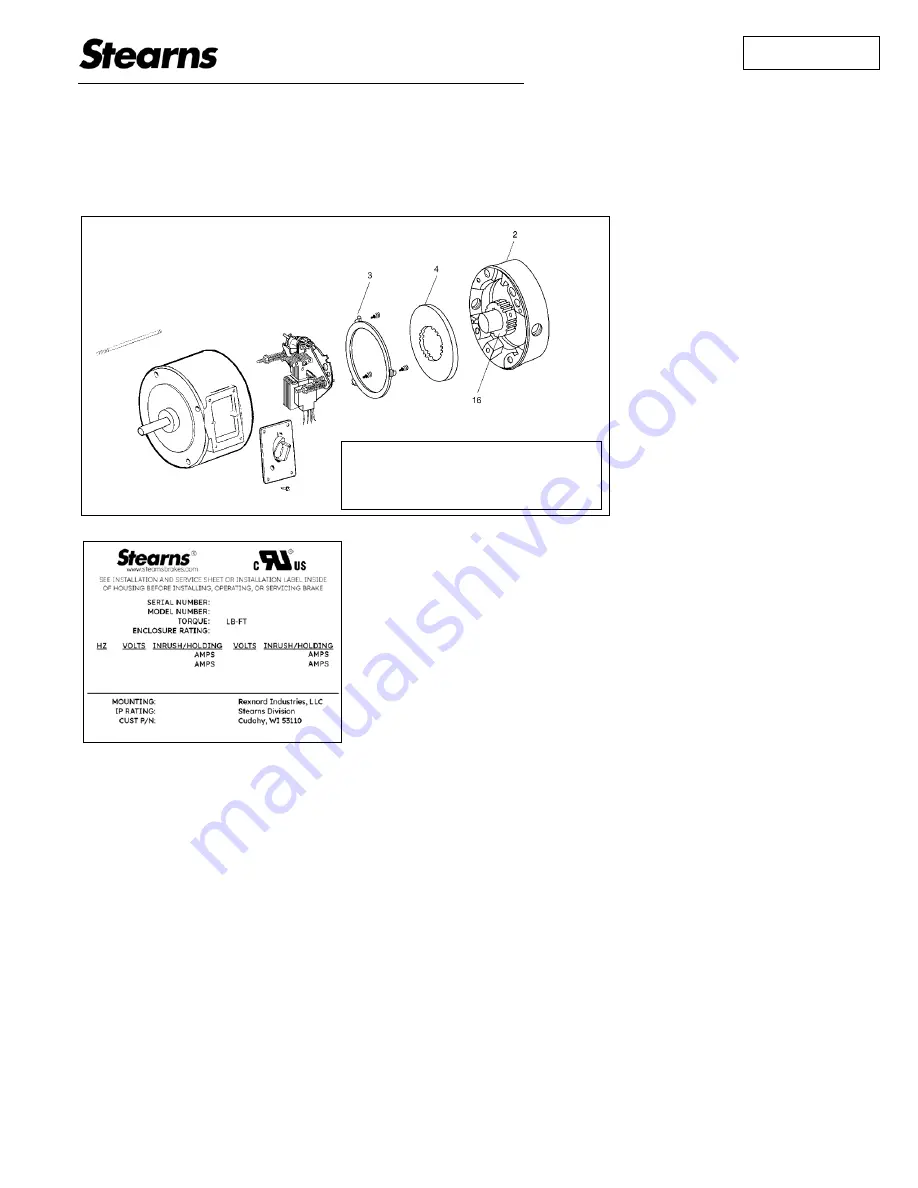
Installation and Service Instructions
for 1-056-700 Series (rev. C)
Double C-Face Coupler
®
Spring-Set Disc Brakes
P/N 8-078-905-69
effective 05/16/2022
Typical Nameplate
Important
Please read these instructions carefully
before installing, operating, or servicing
your Stearns Brake. Failure to comply with
these instructions could cause injury to
personnel and/or damage to property if the
brake is installed or operated incor-rectly.
For definition of limited warranty/liability,
contact Rexnord Industries, LLC, Stearns
Division, 5150 S. International Dr., Cudahy,
WI 53110, (414) 272-1100
Caution
1. Installation and servicing must be
made in compliance with all local safety
codes including Occupational Safety
and Health Act (OSHA). All wiring and
electrical connections must comply with
the National Electric Code (NEC) and
local electric codes in effect.
2. Do not operate the brake in
atmospheres containing explosive
gases or dusts.
3. To prevent an electrical hazard,
disconnect power source before
working on the brake. If power
disconnect point is out of sight, lock
disconnect in the off position and tag to
prevent accidental application of power.
4. Make certain power source conforms to
the requirements specified on the brake
nameplate.
5. Be careful when touching the exterior of
an operating brake. Allow sufficient time
for brake to cool before disassembly.
Surfaces may be hot enough to be
painful or cause injury.
6. Do not operate brake with housing
removed. All moving parts should be
guarded.
7. Installation and servicing should be
performed only by qualified person-
nel familiar with the construction and
operation of the brake.
8. For proper performance and operation,
only genuine Stearns parts should be
used for repairs and replacements.
9. After usage, the brake interior will
contain burnt and degraded friction
material dust. This dust must be
removed before servicing or adjusting
the brake.
DO NOT BLOW OFF DUST using an air
hose. It is important to avoid dispersing dust
into the air or inhaling it, as this may be
dangerous to your health.
a) Wear a filtered mask or a respirator while
removing dust from the inside of a brake.
b) Use a vacuum cleaner or a soft brush
to remove dust from the brake. When
brushing, avoid caus-ing the dust to become
airborne. Collect the dust in a container,
such as a bag, which can be sealed off.
10. Caution!
While the brake is equipped
with a manual release to allow manual
shaft rotation, the motor should not be
run with the manual release engaged,
to avoid overheating the friction disc(s).
General Description
The 56,700 Series coupler is a spring-set,
electronically released brake, containing
either one or more rotating friction discs (4)
driven by a hub (16) mounted on the motor
shaft. The double C-face allows the brake to
directly couple a C-face motor to a C-face
gear reducer.
Operating Principle
Warning!
Do not apply overhung or die load
to brake output shaft.These series contain
one or more friction discs (4) assembled
alternately between the endplate (2) friction
surface, stationary disc(s) (3) and pressure
plate (also called stationary disc) (3). The
stationary disc(s) are restrained from rotating
by being keyed into the endplate. With the
brake released, all disc pack components are
free to slide axially and the friction disc(s) to
rotate.
Brake release occurs when the solenoid coil
is electrically energized, causing the solenoid
plunger to travel a specified distance and
through a lever system, overcoming the
pressure spring force. This action releases
the clamping force on the disc pack, thereby
allowing the friction disc(s) and brake hub to
rotate.
Brake sets and torque is produced when
electric current to the solenoid coil is
interrupted, thereby collapsing the solenoid
magnetic field. The solenoid plunger returns
to its original de-energized position allowing
the lever arm to move forward by virtue of
the compressed torque springs. This action
compresses the disc pack components which
applies a retarding torque to the brake hub
and ultimately restores the brake to a spring-
set static condition.
Tools required for installation and servicing:
3/8” hex wrench
5/16” nut driver
5/16” hex wrench
1/4” screwdriver
3/16” hex wrench
8” adjustable wrench
Figure 1
For replacement parts refer to
sheet part number 8-078-906-07.
Instructions and parts list also
available at
www.stearnsbrakes.com.