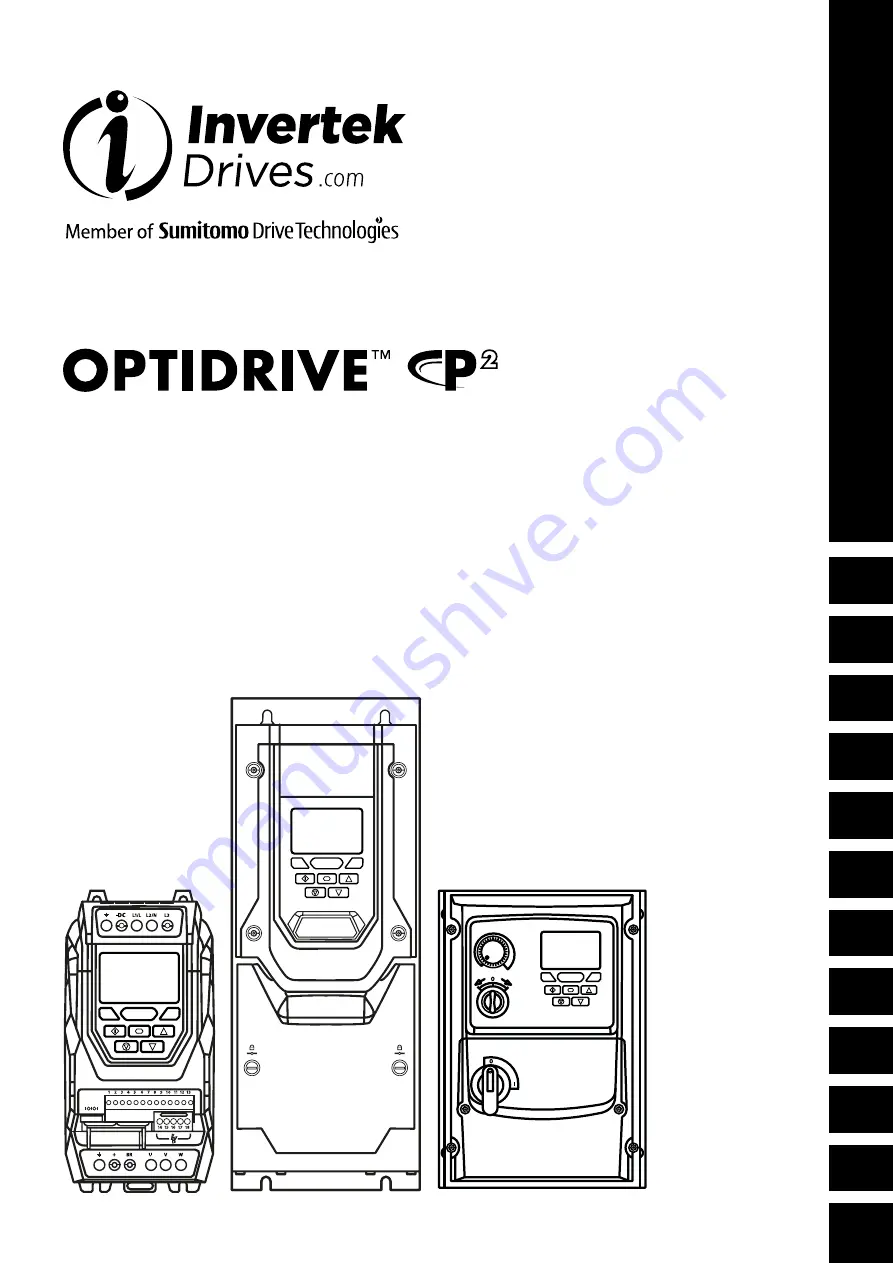
1
4
5
6
7
8
9
10
11
User Guide
AC Variable Speed Drive
0.75 - 250kW / 1 - 350HP
200 - 600V Single and 3 Phase Input
2
General Information
and Ratings
Quick Start Up
3
Mechanical Installation
Electrical Installation
Keypad and Display Operation
Parameters
Extended
Parameters
Serial
Communications
Control Terminal
Functions
Technical Data
Troubleshooting
12
Energy Efficiency Classification