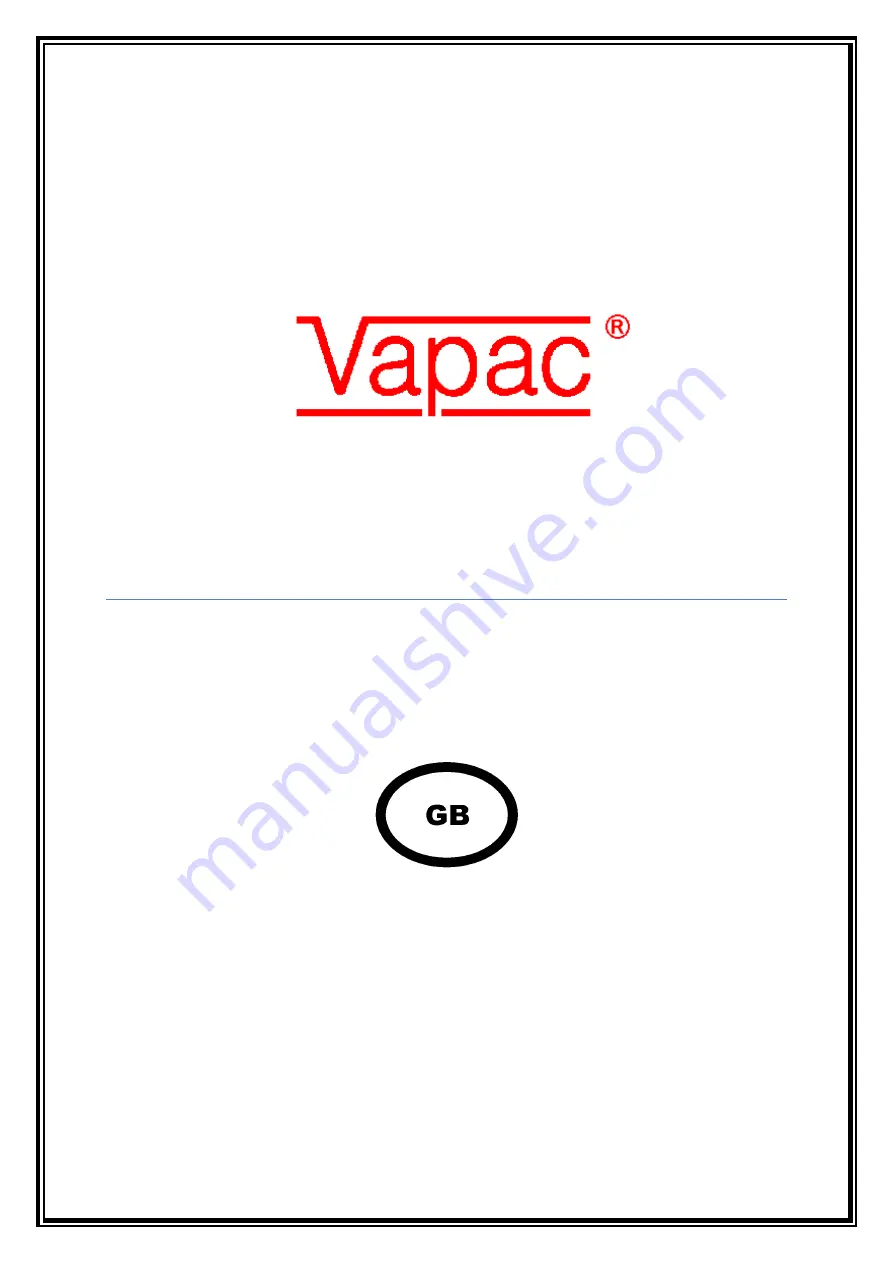
READ & SAVE THESE INSTRUCTIONS.
This manual contains operating information and should be left with the unit.
Model VS--D
Steam Room Unit
Installation & Operating Manual
Edition 1.3.1
Installation in countries covered by EC Directives:
This product meets the requirements of the RoHS Directive 2002/95/EEC
This product will meet the requirements of the Low Voltage Safety Directive 2006/95/EEC
and the EMC Directive 2004/108/EEC when installed in accordance with the instructions
contained in this manual.
Failure to comply with these instructions may invalidate the manufacturer's warranty or any
certificate/declaration of conformance requested to be supplied with the unit.
Summary of Contents for LE18-SR
Page 2: ...Section General Page 2 of 24 18 Feb 2015 ...
Page 9: ...Section 1 Page 9 of 24 18 Feb 2015 Vapac 0 I ...
Page 23: ......