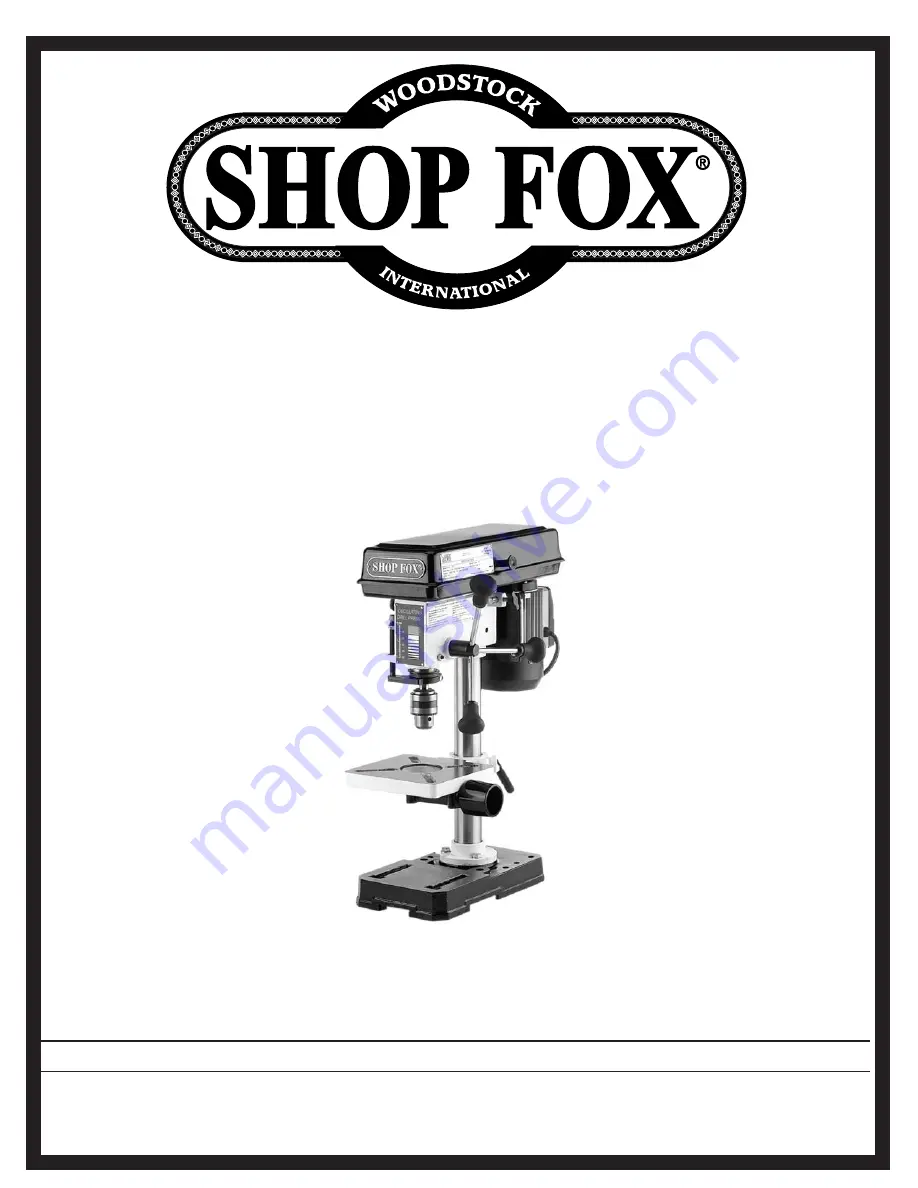
INSTRUCTION MANUAL
MODEL W1667
8
1
⁄
2
"
Oscillating Drill Press
Phone: 1-360-734-3482 • On-Line Technical Support: tech-support@shopfox.biz
COPYRIGHT © 2000 BY WOODSTOCK INTERNATIONAL, INC. REVISED FEBRUARY, 2004.
WARNING: NO PORTION OF THIS MANUAL MAY BE REPRODUCED IN ANY SHAPE OR FORM WITHOUT
THE WRITTEN APPROVAL OF WOODSTOCK INTERNATIONAL, INC.
Summary of Contents for SHOP FOX W1667
Page 21: ... 19 ADJUSTMENTS ...
Page 22: ... 20 ADJUSTMENTS ...
Page 29: ... 27 Parts Diagram MAINTENANCE ...
Page 35: ......
Page 36: ......