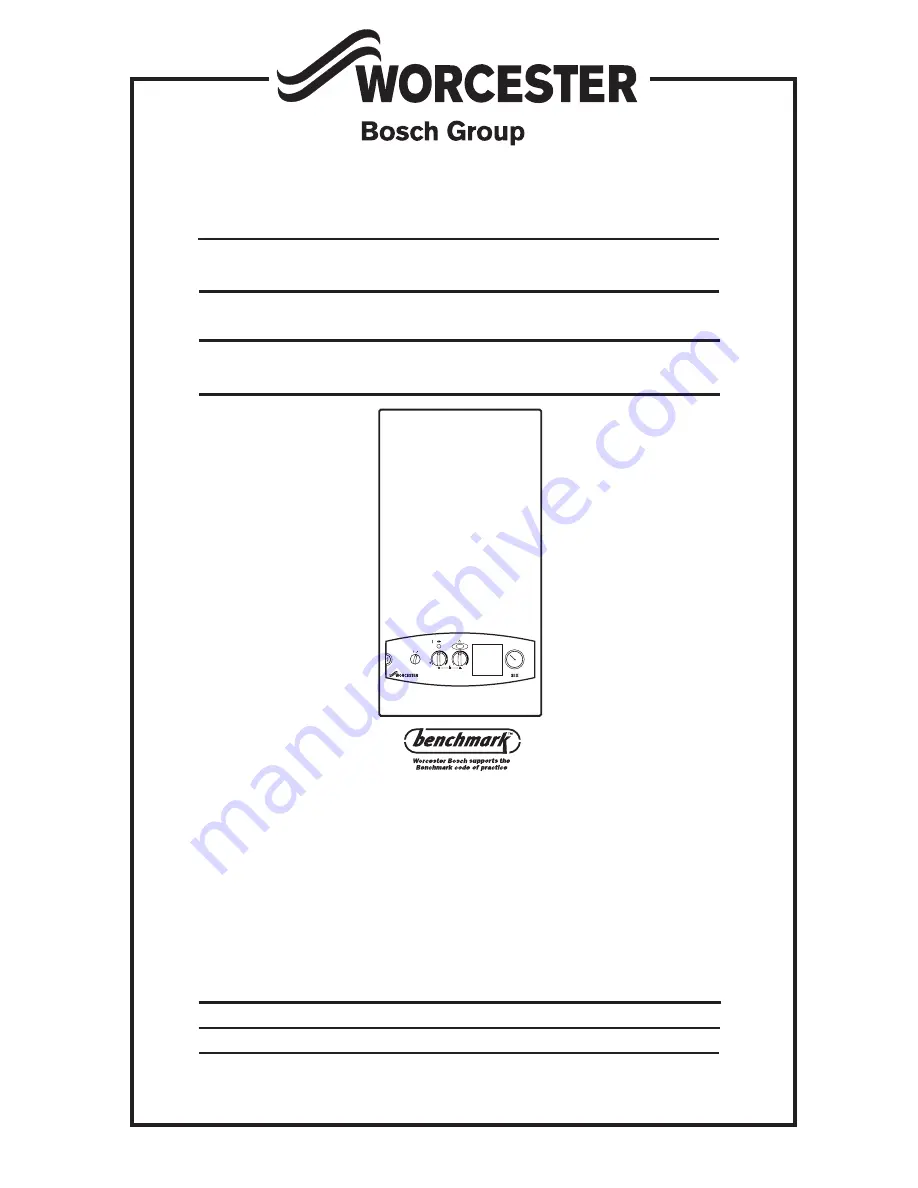
24Si
II /
28Si
II
WALL MOUNTED COMBINATION BOILERS FOR CENTRAL HEATING
AND MAINS FED DOMESTIC HOT WATER
INSTALLATION AND
SERVICING INSTRUCTIONS
This appliance is for use with Natural Gas or LPG (Cat II 2H3P TYPE C12 & C32)
24Si II GC NUMBER 47 311 65 (N.G.)
GC NUMBER 47 311 66 (L.P.G.)
28Si II GC NUMBER 47 311 67 (N.G.)
GC NUMBER 47 311 68 (L.P.G.)
GB/IE
APPLIANCE OUTPUTS
Domestic
Central Heating
Hot Water
24Si II
28Si II 24Si II 28Si II
Minimum 6.9 kW 8.1 kW 6.9 kW 8.1 kW
Maximum 24 kW 28 kW 24 kW 28 kW
IMPORTANT: THESE INSTRUCTIONS APPLY IN THE GB/IE ONLY
AND MUST BE LEFT WITH THE USER OR AT THE GAS METER
It is IMPORTANT to read the instructions before starting work - they have been
written to make the installation easier and prevent hold-ups.