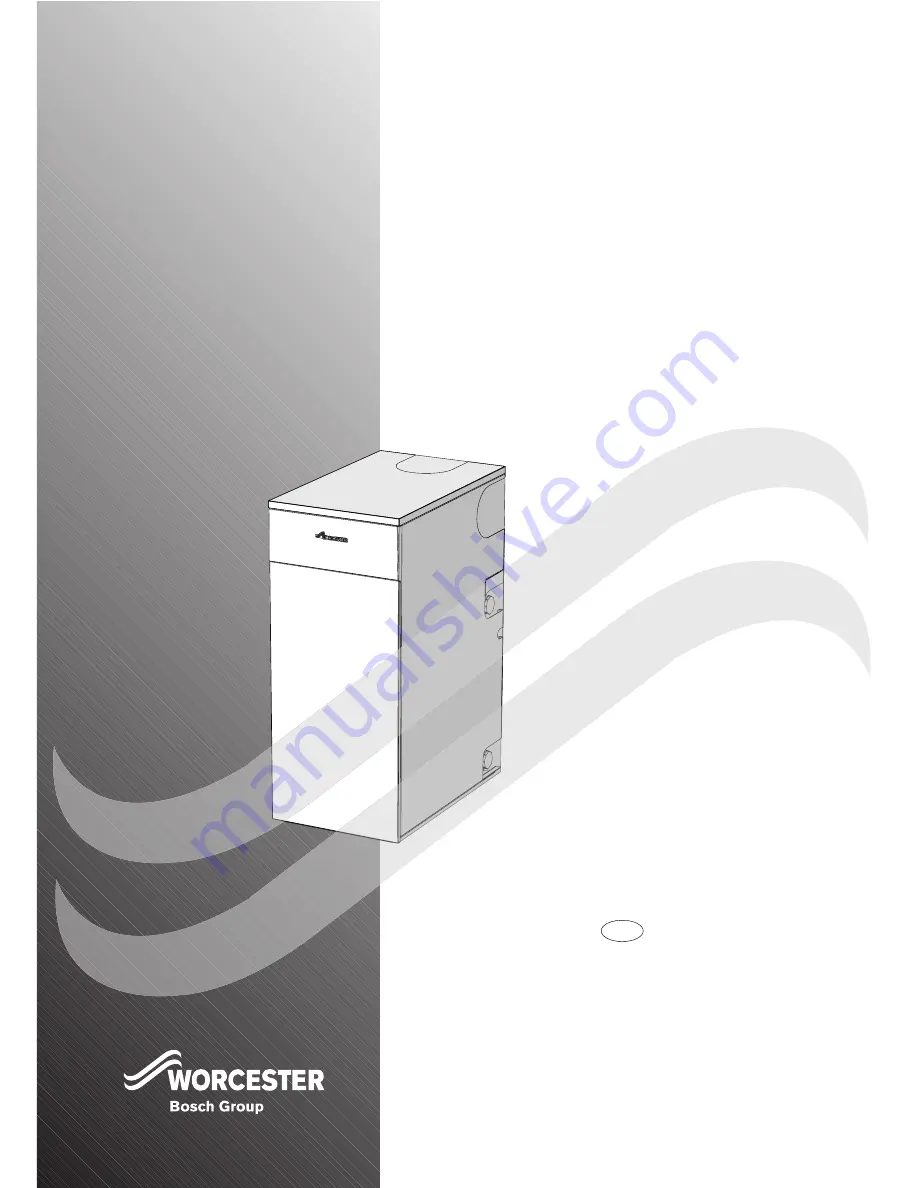
GREENSTAR UTILITY
18/25kW
FLOOR STANDING OIL-FIRED CONDENSING BOILER
CONVENTIONAL FLUE & ROOM SEALED FLUE
FOR FULLY PUMPED OPEN VENT OR SEALED CENTRAL HEATING SYSTEMS AND DOMESTIC
HOT WATER CYLINDERS
THE APPLIANCE IS FOR USE WITH 28 SECOND KEROSENE
ONLY
GB/IE
8-716-106-256a (08.05)
INSTRUCTION MANUAL
INSTALLATION COMMISSIONING
& SERVICING
GB
Patent pending:
Application number 0327645.8
THE APPLIANCE IS FOR USE WITH 28 SECOND KEROSENE
Patent pending:
Application number 0327645.8
THE APPLIANCE IS FOR USE WITH 28 SECOND KEROSENE
ONLY
GB/IE
INSTRUCTION MANUAL
GB