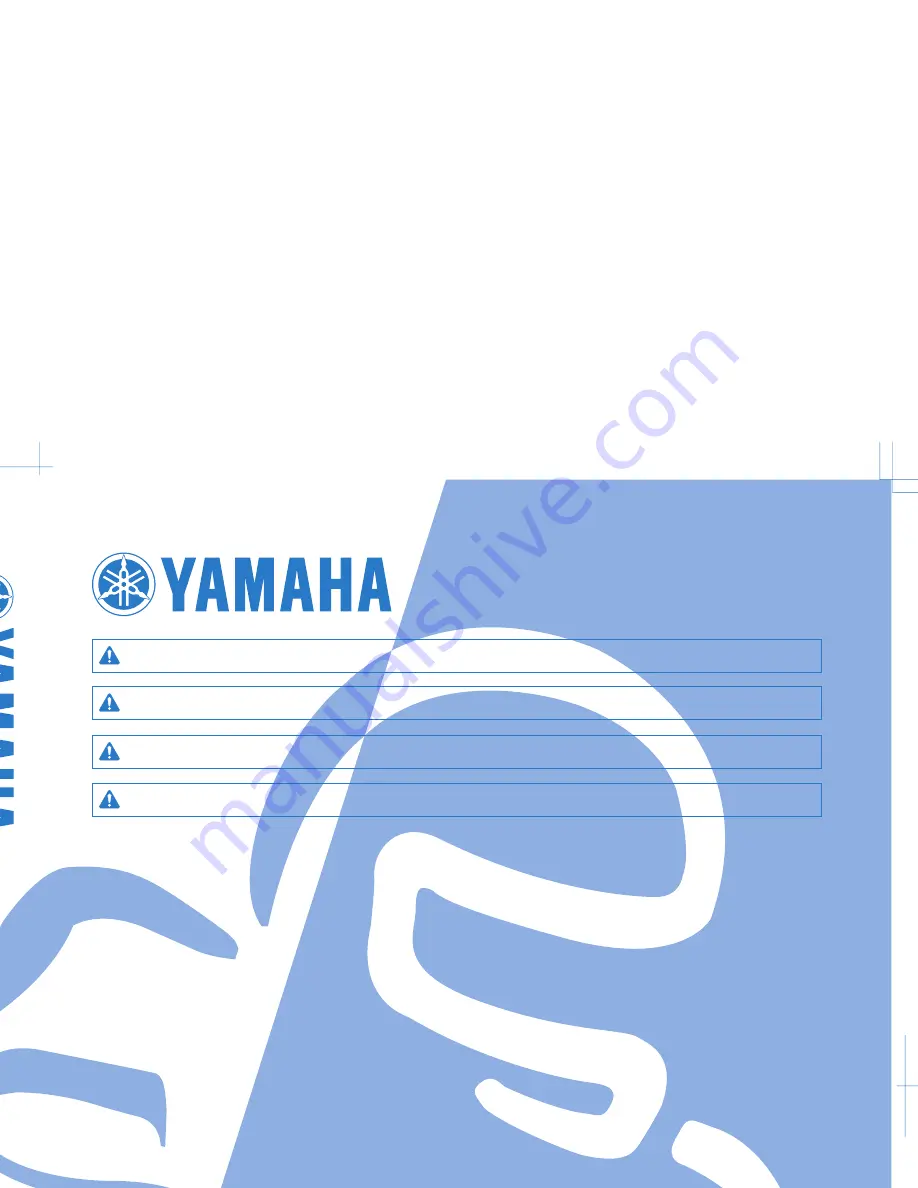
PRINTED ON RECYCLED PAPER
YAMAHA MOTOR CO., LTD.
2500 SHINGAI IWATA SHIZUOKA JAPAN
2009
5XC-28199-35
YZ250F(Y)
OWNER’S SERVICE MANUAL
MANUEL D’ATELIER DU
PROPRIETAIRE
FAHRER- UND
WARTUNGSHANDBUCH
MANUALE DI SERVIZIO DEL
PROPRIETARIO
PRINTED IN JAPAN
2008.05-4.2
×
1 CR
(E,F,G,H)
YZ250F(Y)
2009
Il convient de lire attentivement ce manuel avant la première utilisation du véhicule.
Read this manual carefully before operating this vehicle.
Bitte lesen Sie diese Bedienungsanleitung sorgfältig durch, bevor Sie das Fahrzeug in Betrieb nehmen.
Leggere attentamente questo manuale prima di utilizzare questo veicolo.