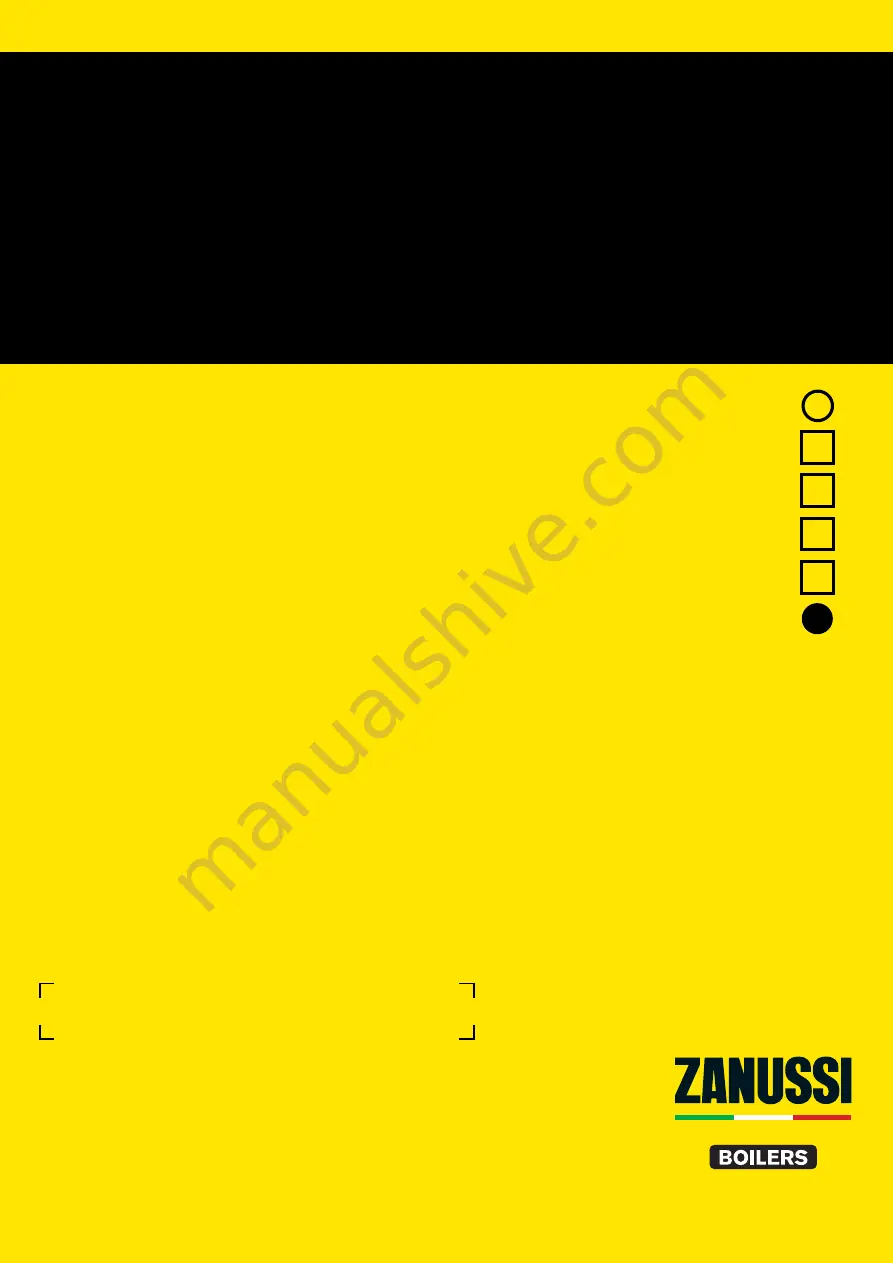
INSTALLATION
AND SERVICING
ULTRA COMBI 30 35
FOR USER GUIDE SEE REVERSE OF BOOK
Manufactured by Ideal Boilers for Zanussi.
When replacing any part on this appliance, use only spare parts that you can be
assured conform to the safety and performance specification that we require.
Do not use reconditioned or copy parts that have not been clearly authorised by Ideal Boilers.
For the very latest copy of literature for specification and maintenance practices visit our website
www.zanussi-boilers.co.uk where you can download the relevant information in PDF format.
April 2016
UIN 214118 A02
Summary of Contents for ULTRA COMBI 35
Page 4: ...4 Installation and Servicing ...
Page 62: ......