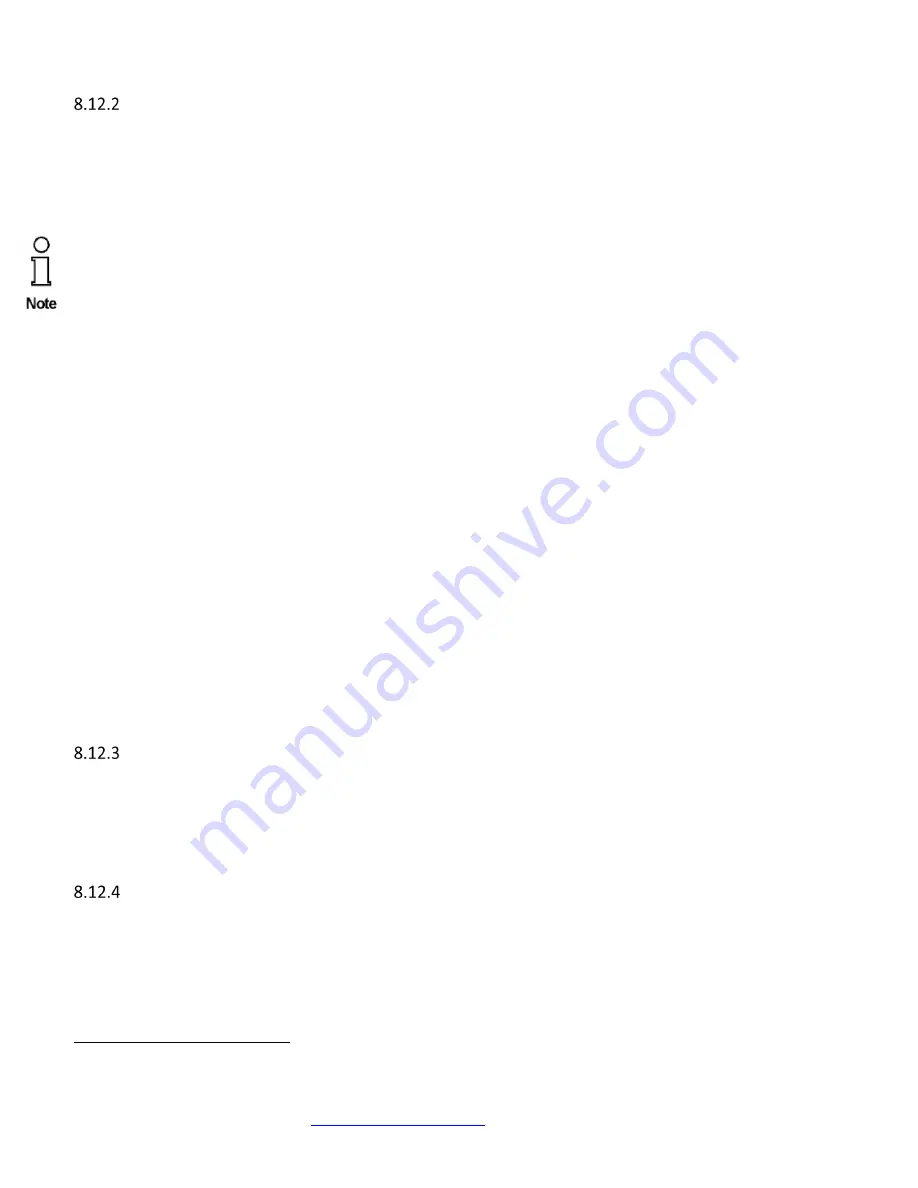
5/12/2017
TECH-538/D.W.O. 23160
Page 91 of 189
Transducer block overview
The Transducer block contains configuration parameters that are used to connect function blocks to the ICoT FF
physical input and output. The Transducer block also performs functions, such as calibration, linearization and
scaling on I/O data to convert it to a form that will be usable on the Fieldbus network.
Note
: see Section 11.2.2 for a diagram of connections between the transducer and the function blocks.
There are some optional parameters that can be configured in order to document the application, like:
•
VALVE_TYPE
, which indicates the type of the valve as defined in the Standard Tables (TN-016). Such
parameters do not affect the operation of the device. See Section 11.4.3 for the complete list of the
Transducer block parameters, including default values.
There are other parameters, however, that may modify the positioner behavior. There are only two mandatory
parameters that must be configured, though:
•
ACT_TYPE:
type of the valve used with the ICoT. The options are: “Rotary”, “Linear” and others.
•
SIGNAL_ACTION
: selects the polarity of the physical output. Default is “0: Increase to Open” which means
‘0’ in the transducer setpoint will energize the physical output. If configured to “1: Increase to Close” the
same ‘1’ in the transducer setpoint will make the physical output de-energize. This can also be seen from
the associated output LED. This is useful when configuring fail-opened or fail-closed valves.
Pneumatics has to be installed accordingly though.
After the Transducer block is properly configured it can be used to control the IP converter output as well as read
the position measurement input.. The Transducer block mode should be set to MAN.
Then, the following parameters can be used to verify the position feedback:
•
WORKING_POS
: the actual measured feedback position.
•
FINAL_POSITION_VALUE
: the actual valve position and status. This is the value sent to be used for an AI
block or as the READBACK in the AO block.
•
The following parameters can be used to control the physical outputs:
•
WORKING_SP
: the final command value to the positioning algorithm. This parameter is read-only.
•
FINAL_VALUE
: the requested valve position and status written by the AO Block.
This parameter can only be written by a properly configured AO block.
Automatic Calibration via Transducer Block
The parameter “PSNR_COMMAND” (sometimes listed as “CALIBRATION_COMMAND”) in the Transducer block
provides a command for the automatic calibration by selecting the option “Arm” and then selecting the option
“Start Auto Cal”. The ICoT will execute the same internal procedures as the command ACAL available in the local
display menu.
Manual Calibration via Transducer Block
The parameter “PSNR_COMMAND” in the Transducer block provides also commands for manual calibration.
shows the commands available in the
MCAL
menu of the local display and their equivalents available in
the Transducer block via the parameter “PSNR_COMMAND”.
24
Although the ICoT’s Transducer Block is not a profiled standard block, it is based on the FF standard positioner Transducer
block defined in the References [11] and [14].