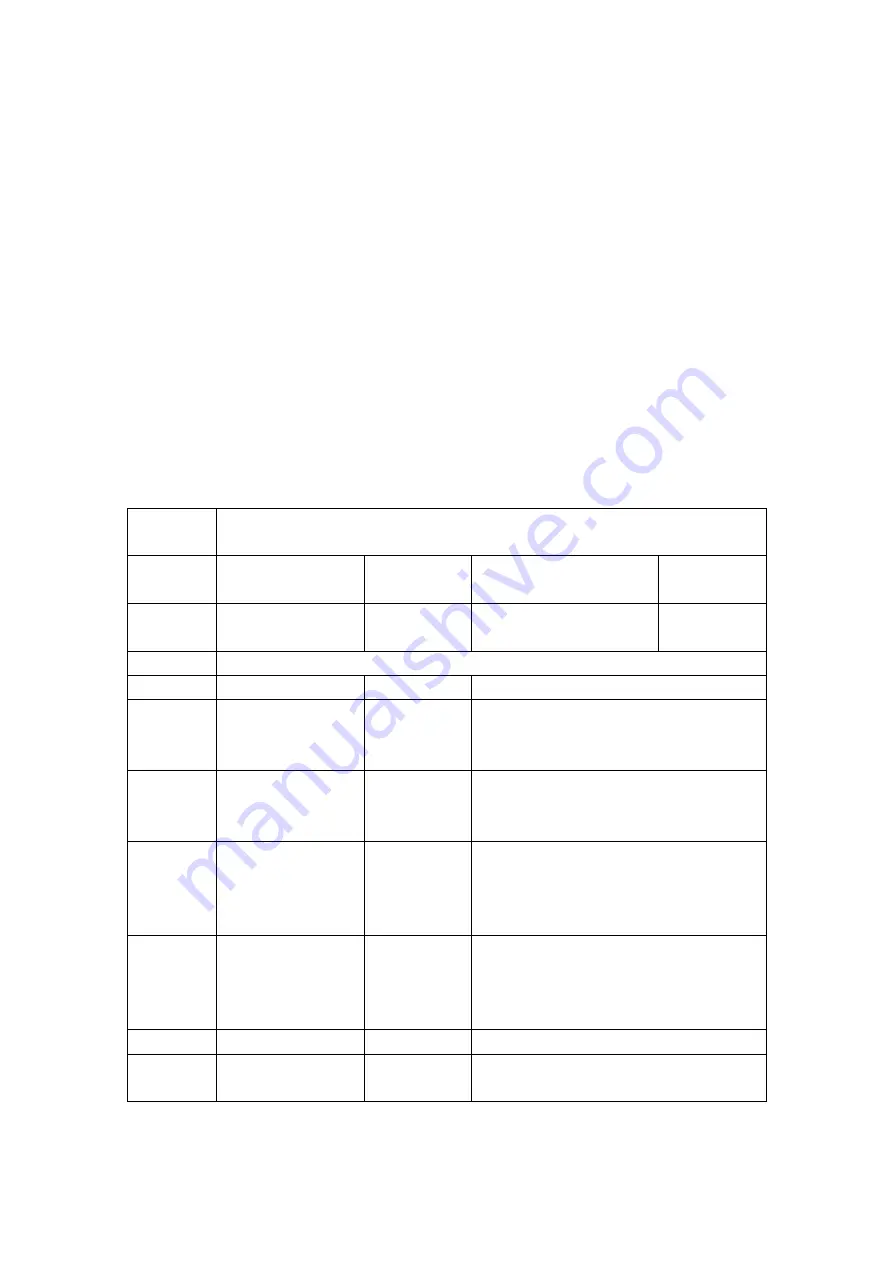
Battery replacement
Turn off the power switch of the HUNTERSE chassis
Press the button lock on the battery replacement panel to open the battery panel
Unplug the currently connected battery interface, respectively (XT60 power connector)
Take out the battery, and pay attention that the battery is not allowed to be bumped and collided during this process
3.3 Development
The CAN communication standard in HUNTER SE adopts CAN2.0B standard, the communication baud rate is
500K, and the message format adopts MOTOROLA format. The linear velocity and steering angle of the chassis
movement can be controlled through the external CAN bus interface; HUNTER SE will feedback the current
movement status information and the status information of the HUNTER chassis in real time. The system status
feedback command includes current vehicle body status feedback, control mode status feedback, battery voltage
feedback and fault feedback. The protocol content is shown in Table 3.1.
Table 3.1 Feedback Frame of HUNTER SE Chassis System Status
Command
Name
System Status Feedback Command
Sending
node
Receiving node
ID
Cycle
(
ms
)
Receive
time-out (ms)
Steer-by-wi
re chassis
Decision-making
control unit
0x211
100ms
None
Data length
0x08
Position
Function
Data type
Description
byte [0]
Current status of vehicle
body
unsigned int8
0x00 System in normal condition
0x01 Emergency stop mode
0x02 System exception
byte [1]
Mode control
unsigned int8
0x00 Standby mode
0x01 CAN command control mode
0x02 Remote control mode
byte [2]
byte [3]
The battery voltage is 8
bits higher
The battery voltage is 8
bits lower
unsigned int16
Actual voltage × 10 (with an accuracy of 0.1V)
byte [4]
byte [5]
The failure information
is 8 bits higher
The failure information
is 8 bits lower
unsigned int16
Refer to remarks [Description of Failure Information]
byte [6]
Reserved
_
0x00
byte [7]
Count check (count)
unsigned int8
0~255 cycle count; every time an instruction is sent, the
count will increase once