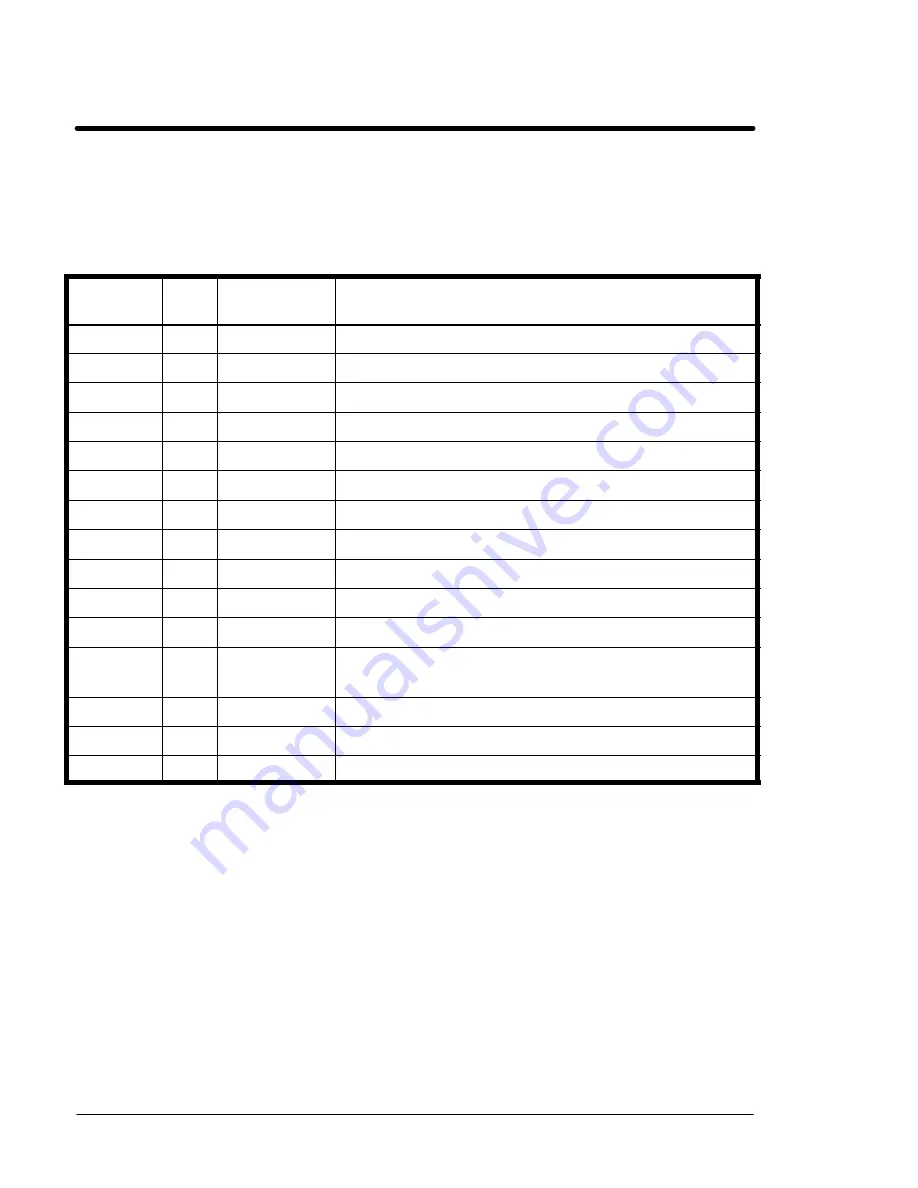
5-4 Software Setup
For 15Hand 21H Inverter controls, use the following registers for
communication. For all other H controls, use the Standard Series H
Area Register Mapping.
Series 15H Specific Area Register Mapping
Register
Address
T#
Read/Write
Description
47000
31
Read Only
Terminal Strip (see NOTE 1)
47001
45
Read Only
Fault Status (0=no fault present)
47002
17
Read Only
Current Actual (100mA RMS)
47003
18
Read Only
Speed Actual (RPM)
47004
19
Read Only
Frequency Actual (.1 Hz)
47005
33
Read Only
Software Revision (ex S15–4.03 is returned as 403)
47006
34
Read Only
Product Series (ex Series 15H returns 15)
47007
35
Read Only
Product Class (5=H)
47008
1
Read/Write
Run Cmd (0=stop, 1=fwd, 2=rev, 3=bipolar)
47009
5
Read/Write
Command Mode (see NOTE 2)
47010
6
Read/Write
Hz Speed Ref
47011
3
Read/Write
Control Source (0=keypad, 1=terminal strip, 2=net-
work)
47012
Reserved
47013
75
Write Only
Digital Output
47014
46
Write Only
Fault Reset (1=execute fault reset)
Notes:
After the fault is cleared (1=execute fault reset), you must send a
stop (run cmd=0) followed by the direction for the run command
again. Otherwise, the motor will not run.
To use register 47008, you must jumper terminals J4–8, J4–9,
J4–10 and J4–17 together to allow the motor to run.
Summary of Contents for Modbus Plus
Page 3: ...ii Table of Contents ...
Page 9: ...2 2 Description ...
Page 15: ...3 6 Installation ...
Page 21: ...4 6 Hardware Setup ...