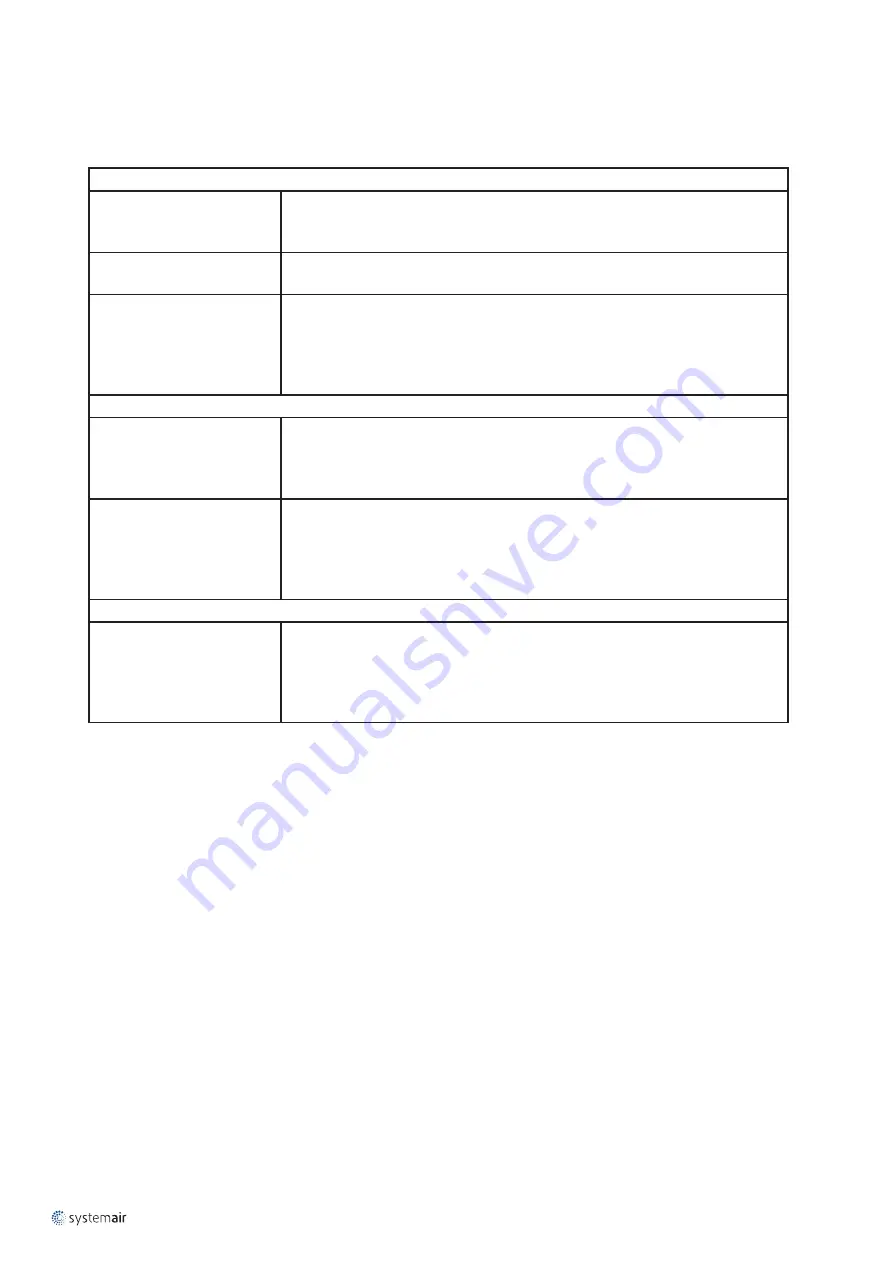
12
|
Systemair NOVA drive 370
7 LED behaviour
The three LEDs in NOVA RHC (red, yellow, green) behaviour is depicted below.
Start/Stop signals
Stopped and ready to start
The inverter indicates it is stopped but ready to start (no faults prevent starting).
In this case the green LED flash slowly (500ms on, 500 ms off). If the inverter
has warnings or errors, then it will not show this.
Running
When the inverter is running, the green LED is ON all the time. If the inverter has
warnings or errors then it will show those instead.
Retrying
When the inverter has been stopped due to a fault and try to start again on its
own, it flash green fast (200 ms on, 200 ms off). It stops flashing when it has
reached the setpoint. As the control strategy is V/f, tolerance for reaching the
setpoint is 0. If the inverter has warnings or errors it will overwrite those and not
show those warnings and errors until the retry has reached the setpoint.
Faults and warnings
Warnings
When the inverter has a warning it flashes the yellow LED as many times as the
warning code and then pauses (400 ms on, 400 ms off, 2000 ms pause at the
end). The action is repeated until the warnings are cleared. If more than one
warning is activated the latest warning is the one shown.
Faults
When the inverter has an error that prevents it from starting then it flashes red
as many times as the error code and then pauses (400 ms on, 400 ms off, 2000
ms pause at the end). The action is repeated until the errors are cleared. If a
warning appears after an error the inverter will still show the latest error as it
has higher priority.
Rotary guard
Rotary guard passed
When the rotary guard passes it shows the red-green-red-green sequence
(200ms each LED). If the inverter has no warnings or faults then this sequence
will override any LED indication immediately. If there are warnings or faults it will
wait for the fault sequence to stop toggling the LEDs indicating the error number
and will show the rotary guard sequence after.
Table 8 – LED behaviour table
8 Fault behaviour
Each error has a maximum number of retries allowed within a 30 minute window. After 30 minutes of no errors the
counts are reset. Errors are only counted when the motor is running or trying to run. Rotary Guard errors do not get
auto-reset after 30 minutes and stay forever until the reset fault command is sent. This is because at low speeds it can
take more than 30 minutes for the error to appear.
When an error occurs, the inverter will stop (except with Modbus communication error) and set the relay. If the inverter
is able to retry a start again (count < maxCount for that error) then it is considered a warning. In this case, the inverter
will inform with the warning LED sequence and will clear the relay when retrying. It will also set the warning bit in
WarningContents. The user must power reset or reset faults to clear the warnings (both LEDs and register). Modbus
communication error will never stop the inverter and will only show as a warning.
When an error has occurred enough that count >= maxCount then the inverter will stop trying to start. In this case it
will blink with the error LED sequence leave the relay set. At this point the inverter must be reset or the fault clear to
start operation again.
A summary of errors is given below.