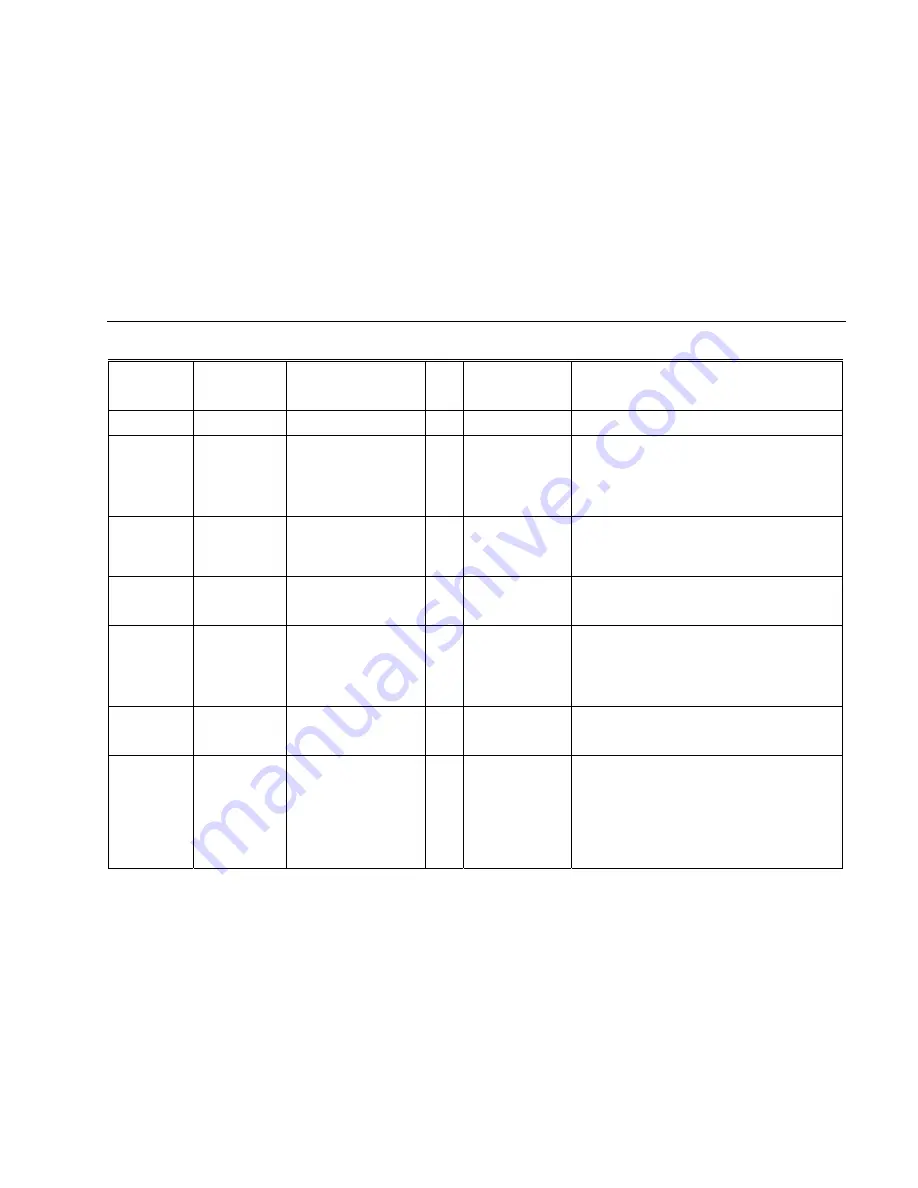
EXCEL 10 FCU CONTROLLER LNS PLUG-INS USER GUIDE
61 EN2B-0285GE51
R0909
Table C4. Output Variables for Excel 10 FCU Controllers.
NV name
field name
engineering units:
English (metric) or states plus
range
digital
state
or
value
default comments
0 to 65535
nvoSensor fan_speed_switch SNVT_lev_disc
ST_OFF
ST_LOW
ST_MED
ST_HIGH
ST_NUL (No Switch)
0
1
2
3
255
This output variable indicates the position of the fan speed switch
ON the wall module.
nvoSensor remote_set_point
SNVT_temp_p
-9 to 9 DDF (-5 to 5 K) for
relative
53.6 to 86°F (12 to 30°C) for
absolute
This output variable is the setpoint from the wall module setpoint
knob and may be absolute or relative depending upon
nciWallMod.set_pnt_knob.
nvoSensor space_temp SNVT_temp_p
0 to 104°F (0 to 40°C)
621.806°F (327.67°C) =
INVALID
This output variable is the measured space temperature.
nvoSensor ub_hard_config
BYTE
INITIAL
W7752D, F
W7752E, G
INVALID
0
4
5
255
INITIAL
(at application restart)
This output variable is used to establish hardware-dependent
factory default configuration settings for the Fan Coil Unit
controller. Note that D and F versions and E, G and J versions
differ only in their supply voltage.
nvoSensorOcc
SNVT_occupancy
OC_OCCUPIED
OC_UNOCCUPIED
OC_NUL (No Sensor)
0
1
255
OC_NUL
(at application restart)
This output variable shows the state of the locally-wired occupancy
sensor, if one is configured by nciFcuConfig.DI1_config. OC_NUL
means no input is available because it is not bound or not
configured by nciFcuConfig.DI1_config.
nvoSpaceTemp
SNVT_temp_p
0 to 104°F (0 to 40°C)
621.806°F (327.67°C) =
INVALID
INVALID
(at application restart)
This output variable is the sensed space temperature at the node
taken from the locally-wired sensor. It is typically bound to
nviSpaceTemp of another node which may not have its own space
temperature sensor but controls the same space. It is also used for
monitoring purposes, showing the current space temperature used
for the control algorithm. nvoSpaceTemp is transmitted
immediately when its value has changed significantly (> 0.5
delta°C). The reported space temperature includes the offset
correction nciWallMod.si_space_temp_zero_cal. If a space
temperature sensor is not connected or is shorted or if
Summary of Contents for Excel 10 W7752D
Page 38: ......