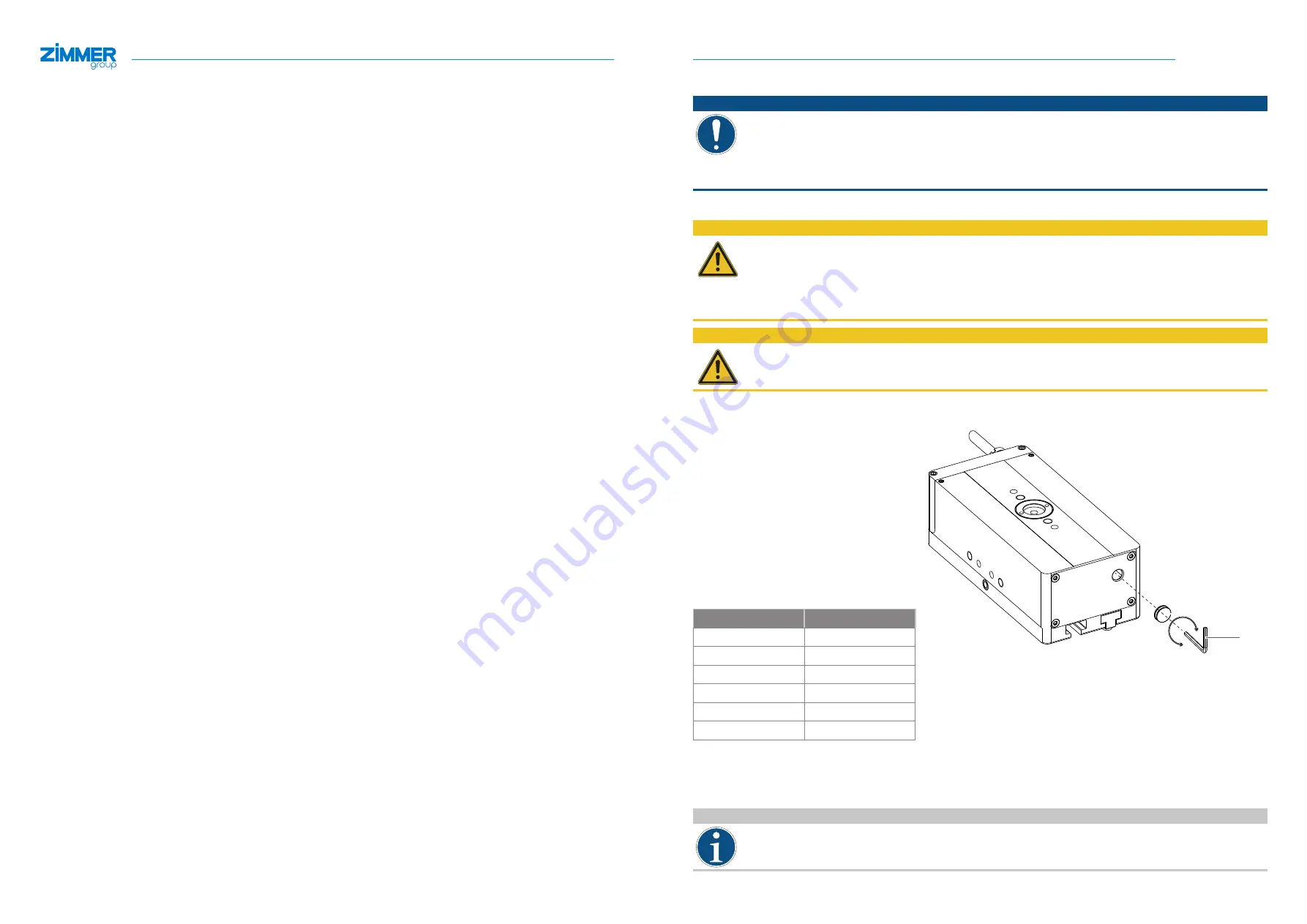
INSTALLATION AND OPERATING INSTRUCTIONS:
GEH6000IL/GED6000IL
INSTALLATION AND OPERATING INSTRUCTIONS:
GEH6000IL/GED6000IL
54
55
EN / 2021-07-28
DDOC00212 / 0
EN / 2021-07-22
DDOC00212 / 0
Zimmer GmbH
•
Am Glockenloch 2
•
77866 Rheinau, Germany
•
+49 7844 9138 0
•
www.zimmer-group.com
Zimmer GmbH
•
Am Glockenloch 2
•
77866 Rheinau, Germany
•
+49 7844 9138 0
•
www.zimmer-group.com
11.21.2 Loading a recipe
The following example code shows how process parameters can be loaded to the internal workpiece recipe.
CASE iStep OF
10:
WorkpieceNo
:= 3;
// Third workpiece recipe is to be loaded
ControlWord
:= 1;
// Begins with the handshake
iStep
:= 20;
// Jump to the next step
20:
IF StatusWord.12 THEN
// Queries the DataTransferOK = TRUE bit from StatusWord,
// this is the response of the gripper to transmitted data
ControlWord
:= 0;
// Reset of the ControlWord
iStep
:= 30;
// Jump to the next step
END_IF;
30:
IF NOT StatusWord.10 THEN
// Query for completion of the data transfer,
// DataTransferOK = FALSE
// Do other things...
// Handshake is completed,
// the parameters from the third recipe are
// now applied to the current process parameters
END_IF;
END_CASE;
12 Operation
NOTICE
In the event of a power failure, for products with -03 in the part number, the gripper jaws remain in their positions
and the gripping force of the product stays constant.
The gripper jaws can be opened manually using the emergency release if the energy supply drops off or there is
a mechanical jam.
►
Please contact Zimmer Customer Service if you have any questions.
12.1 Emergency release of GEH6000IL
CAUTION
Risk of injury due to uncontrolled movement
Risk of injury in the event of uncontrolled movement of the product when the power supply is connected.
►
Switch off the power supply to the product before all work.
►
Secure the power supply against being switched on unintentionally.
►
Check the product for any residual energy that may be present.
CAUTION
Risk of injury in case of non-compliance
►
Disconnect the actuator voltage before pressing the emergency release.
The product features an emergency release that can be mechanically opened with an Allen key in the event of a power
failure.
►
Switch off the power supply.
►
Remove the protective cap to reach the
emergency release.
►
Actuate the emergency release with the
corresponding Allen key.
•
Turning counterclockwise opens the
jaws (toward the BasePosition).
•
Turning clockwise closes the jaws
(toward the WorkPosition).
►
When opening the gripper fingers, make
sure that the workpiece in the product is
secured.
cm
cn
Installation size
Wrench size [mm]
GEH6040IL-03-B
2.5
GEH6040IL-31-B
3.0
GEH6060IL-03-B
2.5
GEH6060IL-31-B
2.0
GEH6140IL-03-B
3.0
GEH6180IL-03-B
3.0
cm
Protective cap
cn
Allen key
INFORMATION
►
Carry out another reference run after any emergency release.
►
Please contact Zimmer Customer Service if you have any questions.