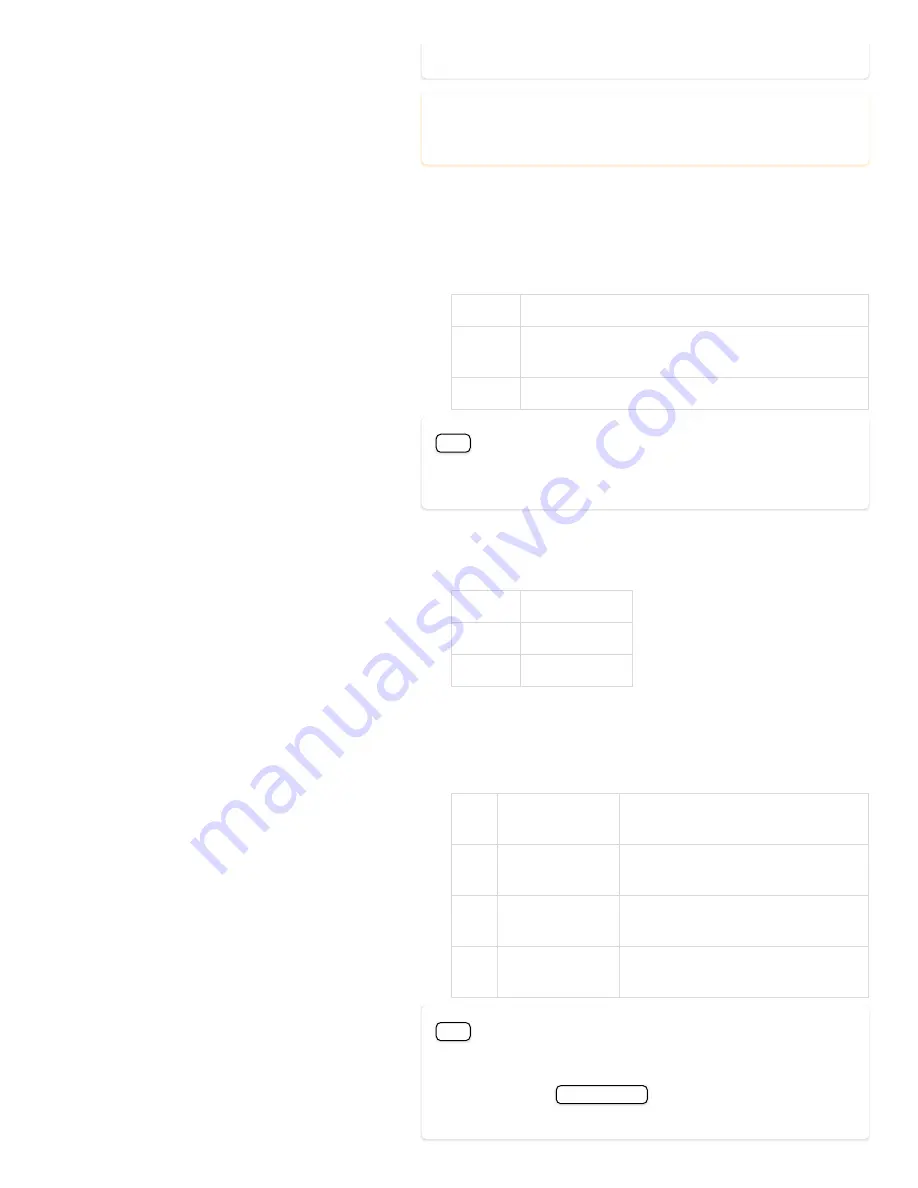
2/22/2018
ROBOTIS e-Manual
http://emanual.robotis.com/docs/en/dxl/x/xm430-w210/
16/34
Manual.)
If Shutdown occurs, LED will flicker every second.(Firmware v41 or
above)
2. 4. 20. Torque Enable(64)
Controls Torque ON/OFF. Writing ‘1’ to this address will turn
on the Torque and all Data in the EEPROM area will be
protected.
Value
Description
0(Default)
Torque OFF(Free-run) and the motor does not generate
torque
1
Torque ON and all Data in the EEPROM area will be locked
Note
Present Position(132) can be reset when Operating
Mode(11) and Torque Enable(64) are updated. For more details,
please refer to the Homing Offset(20) and Present Position(132).
2. 4. 21. LED(65)
Turn on or turn off the LED on Dynamixel.
Bit
Description
0(Default) Turn OFF the LED
1
Turn ON the LED
2. 4. 22. Status Return Level(68)
This value decides how to return Status Packet when
Dynamixel receives an Instruction Packet.
Value
Responding
Instructions
Description
0
PING Instruction
Status Packet will not be returned for all
Instructions
1
PING Instruction
READ Instruction
Status Packet will be returned only for
READ Instruction
2
All Instructions
Status Packet will be returned for all
Instructions
Note
If the ID of Instruction Packet is set to Broad Cast ID(0xFE),
Status Packet will not be returned for READ and WRITE
Instructions regardless of Status Return Level. For more details,
please refer to the
Status Packet
section for
Back to Top ▲