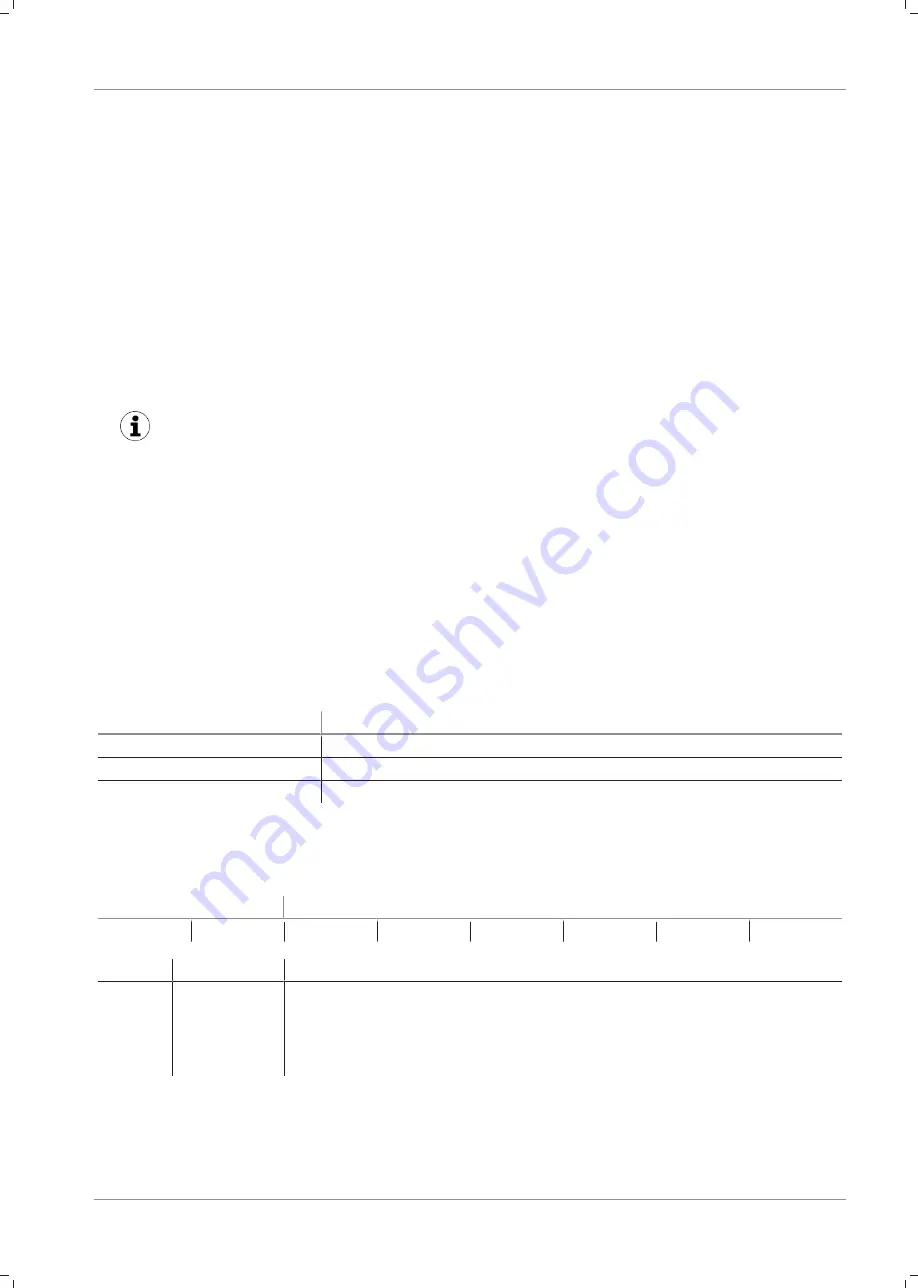
Interfaces
EN-US · 30.30.01.01598 · 02 · 01/18
23 / 74
5 Interfaces
5.1 Industrial Ethernet
The industrial Ethernet interface is used to control the entire SCTMi, set all of the parameters and provide
a wide variety of measurement and analysis data.
The PROFINET, EtherNet/IP or EtherCAT protocol is supported, depending on the design.
5.2 Process Data
The cyclical process data is used to control the ejectors and receive current information reported from the
Compact Terminal SCTMi. From the perspective of the higher-level PLC, there is a difference between in-
put process data (data from the SCTMi) and output process data (data to the SCTMi):
Device description files are available for integration into a higher-level controller.
The process data width is always the same, regardless of how many ejectors are actually on the
SCTMi.
5.2.1 Input Process Data
The input data provides cyclical reporting of a range of information relating to the SCTMi and the individ-
ual ejectors:
•
The SCTMi Device Status in the form of a status traffic light
•
The switching values H1 and H2 for the connected ejectors
•
Error messages from the control unit
•
Condition Monitoring events from the control unit and the individual ejectors
The input process data is 23 bytes long.
Possible Access Types of the Parameters
Access type
Abbreviation
Read only
ro
Write only
wo
Read and write
rw
DEVICE STATUS [ro]
BYTE [0]
DS
res
Bit 7
Bit 6
Bit 5
Bit 4
Bit 3
Bit 2
Bit 1
Bit 0
Bit 5:0
res:
reserved
Bit 7:6
DS:
Device status
00 [green] Device is working optimally
01 [yellow] Device is working, maintenance necessary
10 [orange] Device is working, but there are warnings in the control unit
11 [orange] Device is working, but there are warnings in the control unit