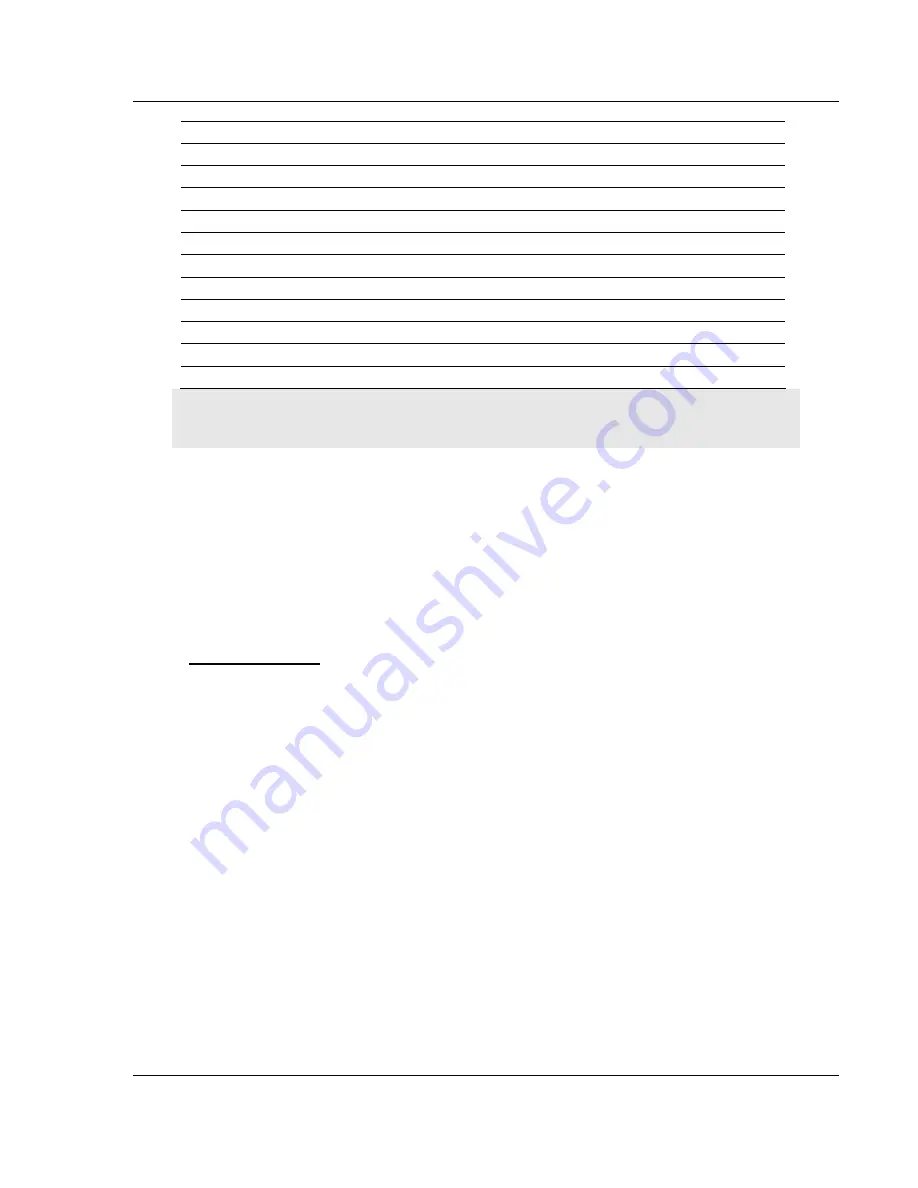
Reference MVI56-DEM
♦
ControlLogix Platform
Honeywell DE Communication Module
ProSoft Technology, Inc.
Page 41 of 80
March 6, 2008
DE Channel
Physical Type
Instrument
7
MV
PV 1 - SMV 3000
8
PV
2
Boundary
Cannot cross boundary with an MV Transmitter
9
SV
ST 3000 Pressure
10
SV
ST 3000 Pressure
11
SV
STT 3000 Temperature
12
SV
STT 3000 Temperature
13
MV
PV 1 - SMV 3000
14 MV
PV
2
15 MV
PV
3
16 MV
PV
4
Multivariable Considerations: The following 'rules' must be followed when integrating
multivariable devices:
1
No instrument can be physically wired to the FTA terminals within the logical
limits of another instrument
2
Cannot cross from Channel 8 to 9 with an MV transmitter, or rollover from
Channel 16 to 1
3
The Tag ID must be identical and non-blank across all logical channels
configured for use by a multivariable device
4
You must perform a Download Command on the physical channel in order to
change the number of PV's being transmitted (DECONFIG can only be
written to the first slot of a multivariable transmitters
Module Power Up
On power up, the module begins performing the following logical functions:
1
Initialize hardware components
o
Initialize backplane driver
o
Test and clear all RAM and shared RAM
o
Test and initialize both DE processors
o
Initialize the serial communication ports
2
Initialize the databases and ports
3
Set up the communication interface for the debug/configuration port
After the module receives the configuration, the module begins receiving and
transmitting messages with devices on the serial networks.