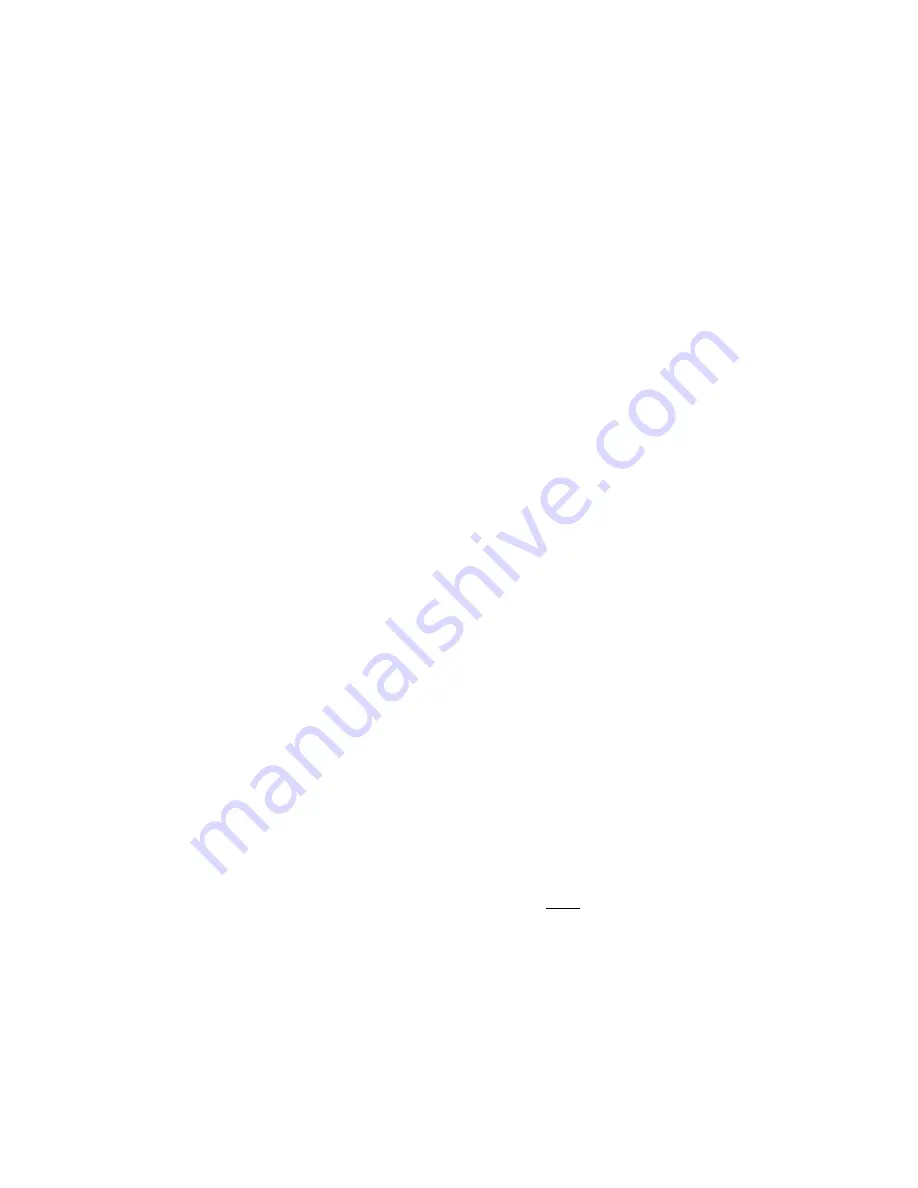
BH8-Series – User’s Manual
support@barrett.com
www.barrett.com
© 2007 Barrett Technology®, Inc.
Document: D3000, Version: AF.00
Page 35 of 82
Parameter:
PTEMP
Name:
Peak Temperature
Purpose:
The maximum temperature ever experienced by this hand
Values:
0 to 1250
Default:
N/A
Notes:
This value is never reset; it is maintained through power failures and firmware
downloads.
Parameter:
UPSECS
Name:
Uptime Seconds
Purpose:
The total power-up time for this hand.
Values:
0 to 4 billion
Default:
N/A
Notes:
This value is never reset; it is maintained through power failures and firmware
downloads. The parameter can accommodate 136 years of power-up time before
rolling over.
Parameter:
SN
Name:
Serial Number
Purpose:
The serial number of the hand.
Values:
N/A
Default:
N/A
Notes:
This value is never reset; it is maintained through power failures and firmware
downloads. Hands upgraded to firmware version 4.2 in the field will have a
serial number of 0.
5.4.3
Advanced
Parameter:
LFDPD
Name:
Loop Feedback Delta Position Discard
Purpose:
If non-zero, then in RealTime mode any position change that cannot be sent in a
delta position datum is discarded. If zero, then any unsent position change is
accumulated for transmission in the next cycle.
Values:
0, 1
Default:
0
Notes:
5.5 Termination Conditions for Movement Commands
There are eight commands in Supervisory mode that control finger motion:
•
Position commands, absolute:
M and HOME
•
Position commands, relative:
IO, IC.
•
Velocity commands with ramp-down at target limits:
O, C
•
Velocity commands with control of motor torque at stall:
TO, TC
In all cases, the command terminates and returns when, for every motor specified in the command,
one of the following termination conditions applies:
Case 1: Motor stalls because obstacle(s) stop the motion. The obstacles include foreign objects as
well as joint stops and other fingers.
•
When a motor stalls, the controller will continue driving it for TSTOP milliseconds, after
which a termination condition occurs.
•
If HOLD is false, the motor is then turned off; if HOLD is true, the motor is servoed to
maintain this position.