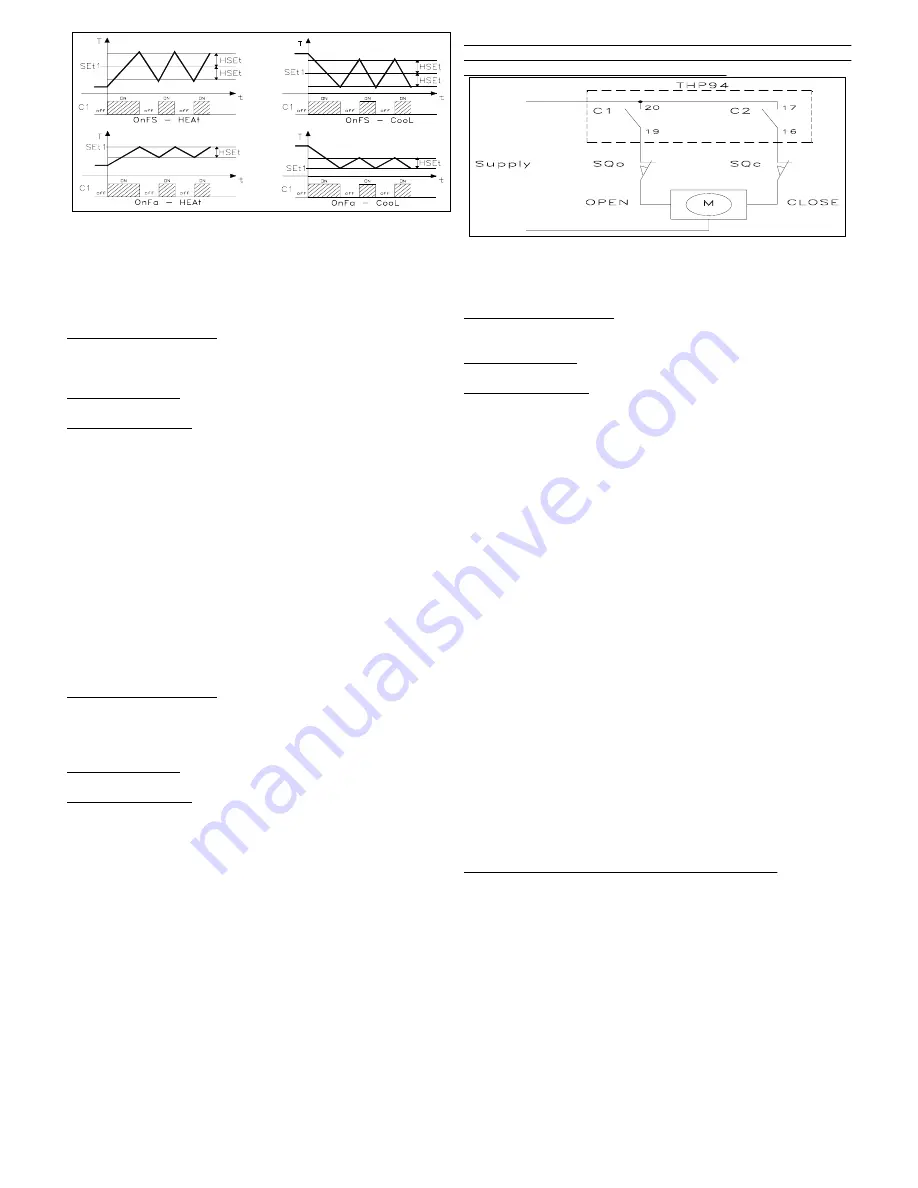
4.5 - SINGLE ACTION PID CONTROL (C1)
The PID single action control mode acts setting parameter "Cont" = "Pid"
and works on C1 output depending on the set point ("SEt1"), on the
functioning mode ("FunC") and on the control algorithm programmed.
The PID algorithm of the instrument is provided to program the following
parameters:
For PROPORTIONAL term :
"Pb"
- Proportional Band,
"rS"
- Manual reset
"tcr1"
- Output C1 Cycle time
For INTEGRAL term:
"Int"
- Integral time
For DERIVATIVE term:
"dEr"
- Derivative time
4.6 - DOUBLE ACTION PID CONTROL (C1,C2)
This kind of action can happen only when the instrument has both control
outputs (C1 and C2) and it has been defined the output C2/A4 functioning
to be used as C2 (par. "C2" = "-Pid"). This kind of regulation is used to
control installations where there's an element which causes a positive
increment (ex. heater) and an element which causes a negative increment
(ex. cooler). With "Func" parameter will be decided C1 output functioning,
while C2 output will automatically works in the opposite way. For
example, if "Func" ="HEAt" to C1 output will be connected the positive
increment element (ex. heater) while to C2 output will be connected the
negative increment element (ex. cooler). PID double action mode acts,
therefore, on C1 and C2 outputs and depends on Set point ("SEt1") and on
control algorithm programmed.
The PID algorithm of the instrument is provided to program the following
parameters:
For PROPORTIONAL term :
"Pb"
- Proportional Band
"rS"
- Manual reset
"tcr1"
- Output C1 Cycle time
"tcr2"
- Output C2 Cycle time
For INTEGRAL term:
"Int"
- Integral time
For DERIVATIVE term:
"dEr"
- Derivative time
And furthermore the parameter
"Prat"
(Power Ratio), on which it's
necessary to set the ratio between power of the element controlled by C2
output and power of the element controlled by C1 output. If ever the
parameter "Prat" is = 0, C2 output is deactivated and the regulator behave
exactly as a PID single action, through C1 output.
4.7 - PID CONTROL FOR MOTORISED ACTUATORS (C1,C2)
This kind of control it's used to control the plants equipped with motorised
actuators, with opening and closing controls and that without commands
remain in the reached point. This kind of action can happen only when the
instrument has both control relay outputs (C1 and C2) and it has been
defined the output C2/A4 functioning, to be used as C2 motorised actuators
control (par. "C2" = "3Pt"). In this kind of regulation the par. "Func" has
to be programmed as "HEAt" so that from C1 output depends the opening
command while from C2 output depends the closing command of the
actuator. The control system used, doesn't need a retraction to establish the
actual position of the actuator because this position is represented by the
integral contribution.
When the actuator is not equipped with stroke-end safety contacts, that
stop the action at travel end, it's necessary to equip the plant with these
stroke-end (SQo, SQc) as shown in picture below :
The PID control mode for motorized actuactors works on C1 and C2
outputs depending on the set point ("SEt1"), and on the programmed
control algorithm which foreseen the programming of the following
parameters:
For PROPORTIONAL term :
"Pb"
- Proportional Band
"rS"
- Manual reset
For INTEGRAL term:
"Int"
- Integral time
For DERIVATIVE term:
"dEr"
- Derivative time
Other parameters are :
-"tcor" :
Travel time. It's the time, expressed in seconds, needed by the
actuator to switch from "all opened" to "all closed" position
.
- "SHrl":
Minimum regulation value. It's the value that the regulation (in
%) has to have reached before having effect on the output. It is used to
avoid that the control intervenes too frequently.
- "dbEr":
Dead zone. It's the zone around the Set point, on which the
control output are not activated. The actuator is not activated when the
process value is included into [SEt1 - dbEr ... SEt1+ dbEr].
- "PoSi":
Positioning at Switching on. It's the position that has to assume
the actuator when the instrument is switched on. Can have the following
values :
no = the actuator remains where it is
OPEn = the actuator reaches the "all opened" position
CloS = the actuator reaches the "all closed" position
If the options "OPEn" and "CloS" are programmed, at the switching on
display will be indicated "SEt Flot" and the regulator will active the C1
output (if "OPEn") or C2 (if "CloS") as long as time programmed on par.
"tcor", afterwards the control will begin.
4.8 - AUTOTUNING AND SELFTUNING FUNCTION
S
The instrument has PID parameters factory programmed with generic
values.If ever these parameters should result to be unsuitable for a correct
process control, it would be advisable to start AUTOTUNING or SELFTU-
NING function in order to perform an automatic PID parameters tuning.
The AUTOTUNING function calculates PID parameters through a tuning
cycle at the end of which the parameters are stored and remain constant
during regulation. The SELFTUNING function (rule based algorithm
named "IN TUNE") monitorizes the process continuously and calculates
PID parameters when necessary.
To enable the AUTOTUNING function procedeed as follows:
1) Program and active the desired "Set point".
2) Program par. "Cont" = "Pid".
3) Program par. "Func" depending on the process to be controlled,
through C1 output. If the instrument control a motorised actuator set
"HEAt".
4) Program, if present, par. "C2" = "-Pid" if the instrument control a plant
with double action or "3Pt" if the instrument control a 3 point motorised
actuator.
5) If the instrument control a motorised actuator, program on par. "tcor"
the actuator travel time, expressed in seconds.
6) Program par. "SELF" as "no".
7) Program par. "Auto" as :
- "FaSt" if it's desired to have a fast tuning of the process during the
reaching of the Set Point. It's to be underlined that the "FAST" tuning is
TECNOLOGIC - THP 94
USER MANUAL (I - GB) - Vr. 05 - ISTR 01195 - PAG. 15