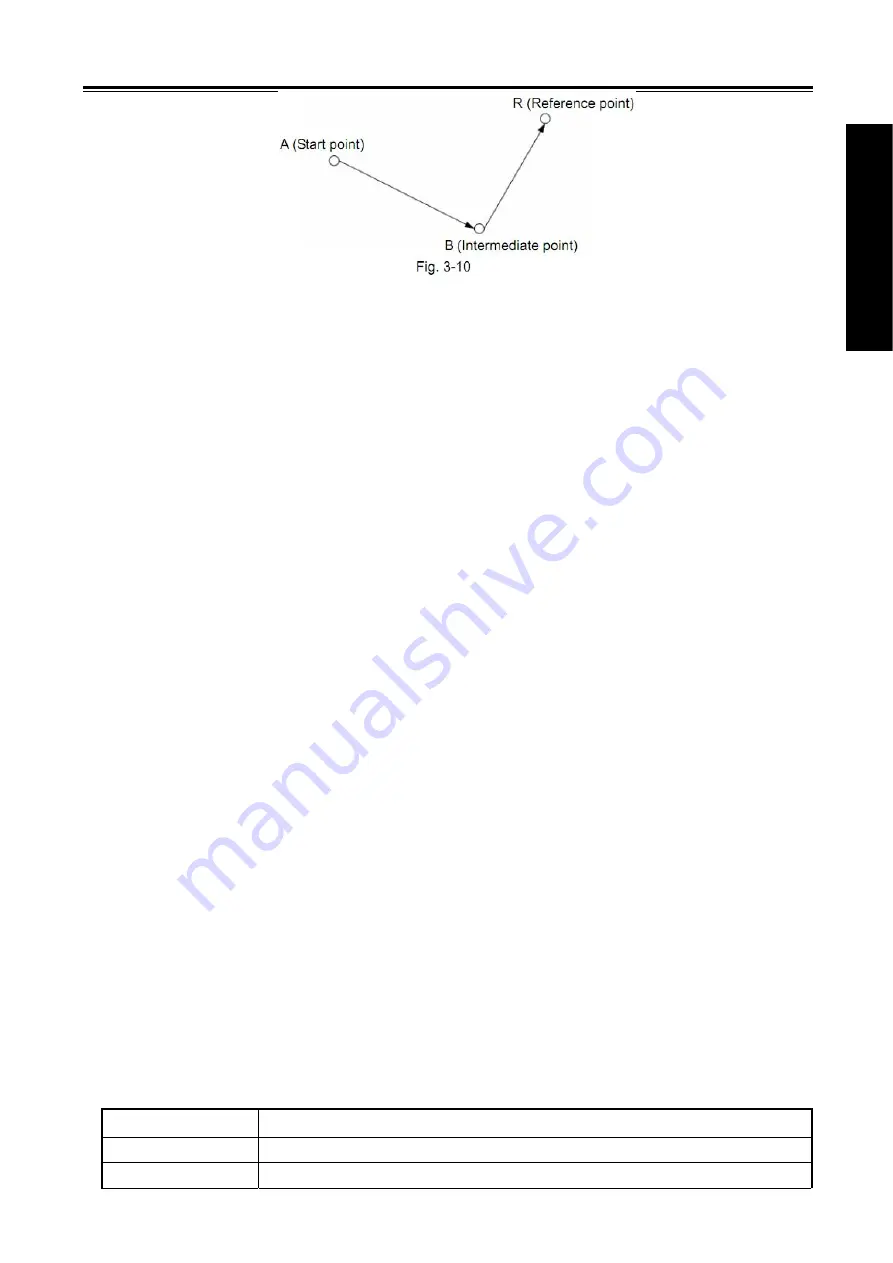
Chapter 3 G Command
47
I Programming
Note
:
z
After power-on, if G28 is executed prior to the manual machine zero return, the process of
G28 machine zero return should be consistent with manual machine zero return, and the
deceleration signal and one-rotation signal should be detected. The G28 machine zero return
hereafter will not detect the deceleration signal and one-rotation signal, but directly position
to zero point.
z
During the process of point A
→
B and B
→
R, the two axes move at two independent speeds,
therefore, the paths may not be linear.
z
After the execution of G28 machine zero return, the bit 7 of parameter No.13 decides
whether cancel cutter compensation or not.
z
In compensation mode, if command G28 is specified, the compensation will be cancelled in
the intermediate point. The compensation mode is cancelled automatically after reference
point return.
z
If zero point switch is not equipped on the machine tool, G28 command and machine zero
return are disabled.
z
The intermediate point can only be established during the movement from the intermediate
point to the reference point which is followed the movement from the start point to the
intermediate point.
z
After the modification of parameters which set the zero return point, manual reference point
return is necessary; G28 command can be executed later.
z
3.12 Return from Reference Point G29
Format:
G29 X_ Y_ Z_;
Function:
When a rapid traverse is performed from the current point to mid point, it positions to the
specified position by X, Y and Z at the rapid traverse rate.
Explanation:
X: The absolute coordinate of aim point in X axis is indicated by G90; the aim point
increment against the mid point in X axis is indicated by G91;
Y: The absolute coordinate of aim point in Y axis is indicated by G90; the aim point
increment against the mid point in Y axis is indicated by G91;
Z: The absolute coordinate of aim point in Z axis is indicated by G90; the aim point
increment against the mid point in Z axis is indicated by G91;
One of the command address X, Y and Z or all of them can be omitted, see the following figure:
Command
Function
G29
X,Y and Z axes are in the original position, the next block continued
G29 X
Only X axis performs the command returning from the reference point
Summary of Contents for 980MDc
Page 19: ...GSK980MDc Milling CNC User Manual XVIII ...
Page 20: ...1 I Programming Programming Ⅰ ...
Page 21: ...GSK980MDc Milling CNC System User Manual 2 I Programming ...
Page 139: ...GSK980MDc Milling CNC System User Manual 120 I Programming ...
Page 191: ...GSK980MDc Milling CNC System User Manual 172 I Programming ...
Page 192: ...173 Ⅱ Operation Ⅱ Operation ...
Page 193: ...GSK980MDc Milling CNC System User Manual 174 Ⅱ Operation ...
Page 200: ...Chapter 1 Operation Mode and Display 181 Ⅱ Operation ...
Page 201: ...GSK980MDc Milling CNC System User Manual 182 Ⅱ Operation ...
Page 249: ...GSK980MDc Milling CNC System User Manual 230 Ⅱ Operation ...
Page 253: ...GSK980MDc Milling CNC System User Manual 234 Ⅱ Operation ...
Page 259: ...GSK980MDc Milling CNC System User Manual 240 Ⅱ Operation ...
Page 265: ...GSK980MDc Milling CNC System User Manual 246 Ⅱ Operation ...
Page 293: ...GSK980MDc Milling CNC System User Manual 274 Ⅱ Operation ...
Page 295: ...GSK980MDc Milling CNC System User Manual 276 Ⅱ Operation ...
Page 319: ...GSK980MDc Milling CNC System User Manual 300 Ⅱ Operation ...
Page 320: ...301 Ⅲ Installation Ⅲ Installation ...
Page 321: ...GSK980MDc Milling CNC System User Manual 302 Ⅲ Installation ...
Page 345: ...GSK980MDc Milling CNC System User Manual 326 Ⅲ Installation ...
Page 391: ...GSK980MDc Milling CNC System User Manual 372 Ⅲ Installation ...
Page 392: ...Appendix 373 Appendix Appendix ...
Page 393: ...GSK980MDc Milling CNC System User Manual 374 Appendix ...
Page 394: ...Appendix 375 Appendix Appendix 1 Outline Dimension of GSK980MDc L N ...