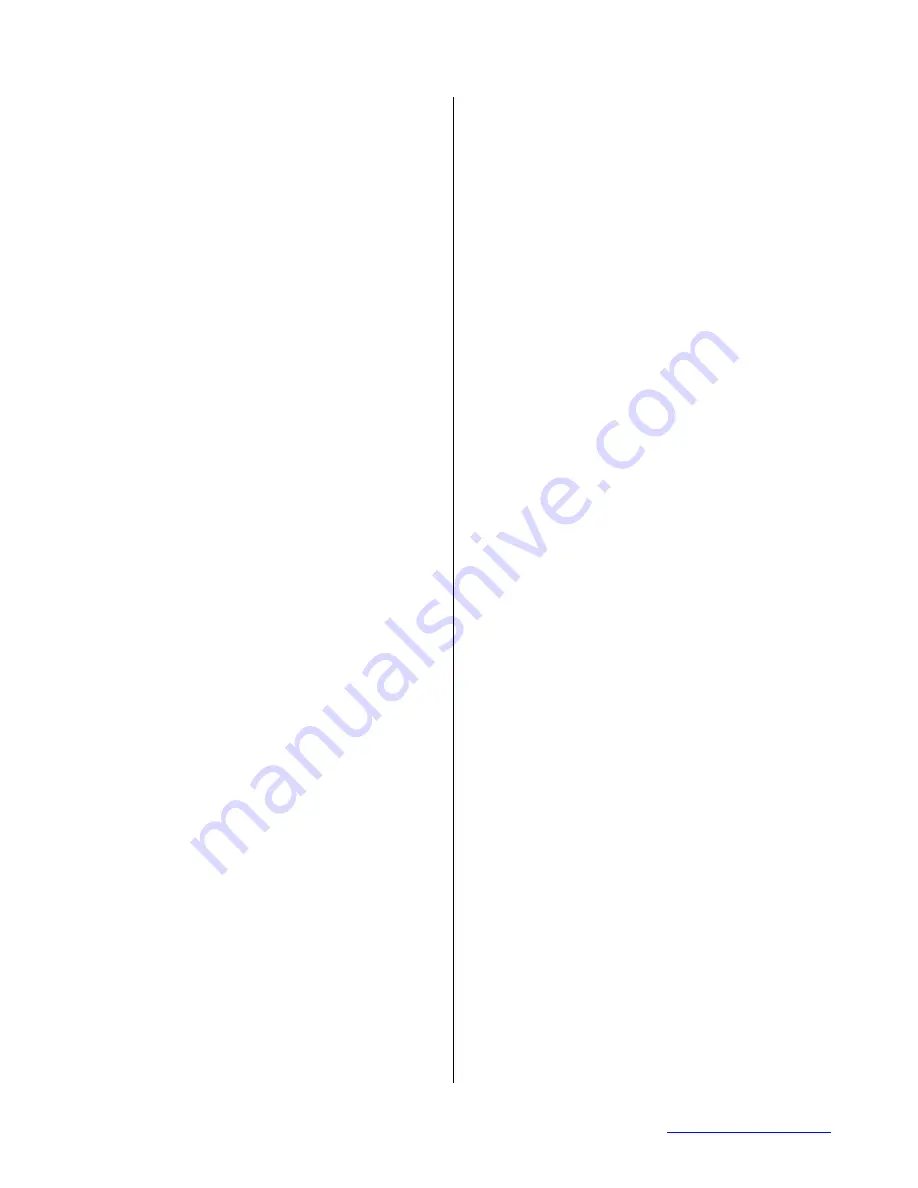
SERIES IP1K110 INDUSTRIAL I/O PACK RECONFIGURABLE DIGITAL I/O MODULE
__________________________________________________________________________________________
- 3 -
Acromag, Inc. Tel:248-295-0310 Fax:248-624-9234 Email:solutions@acromag.com
http://www.acromag.com
The example design supplied with the IP1K110 is provided as
a VHDL file for Altera’s Max+Plus II or Quartus II software. The
example design includes an IP bus interface to ID space, IO
space and Interrupt space. IO space is used to access a 64K x
16 RAM array, control field data I/O, and control a clock
generation chip.
The IP1K110 utilizes state of the art Surface-Mounted
Technology (SMT) to achieve its high channel density and is an
ideal choice for a wide range of industrial control and monitor
applications that require high-density, high-reliability, and high-
performance at a low cost.
KEY IP1K110 FEATURES
•
Reconfigurable Altera FPGA
–
In system configuration of a
100,000 gate FPGA is implemented via the IP bus interface.
This provides a means for implementation of custom user
defined digital designs.
•
IP Bus Interface –
The Altera FPGA is directly connected to
all IP bus logic signals. Custom designs can thus support
all IP module access types including ID, I/O, Interrupt,
Memory, and DMA.
•
High Channel Count Digital Interface
– Differential and
TTL interface options are allowed. Interfaces with up to 24
differential, or a mix of 12 differential and 24 TTL, or up to 48
TTL digital input/output channels.
•
Channel Input/Output Control
– The bidirectionality of the
TTL digital channels is controlled in groups of 8 channels.
The bidirectionality of the differential digital signals is
controlled in groups of 4 channels.
•
Long Distance Data Transmission
– Data transmission
with RS485/RS422 Transceivers allow up to 32 nodes and
up to 4000 feet of transmission cable.
•
64K x 16 SRAM –
A 64K x 16
static random access
memory (SRAM) is directly accessed by the Altera device.
Custom user defined design logic for the Altera FPGA will
permit use of the SRAM as FIFO memory, or single port
memory as required by the application.
•
Example Design Provided –
Example VHDL design which
includes implementation of the IP bus interface and control
of digital I/O with software programmable Interrupts is
provided.
•
Clock Speed –
Supports an 8 or 32 MHz IP bus clock
speed.
•
Programmable Clock Generator –
A clock generator IC is
provided for applications requiring a custom user specified
clock frequency. The clock generator can be programmed
to any desired frequency value between 250KHz and
100MHz.
•
No Configuration Jumpers or Switches
– All configuration
is performed through software commands with no internal
jumpers to configure or switches to set.
•
Power Up & System Reset is Failsafe
– For safety, all
channels are configured as input upon power-up and after a
system reset.
INDUSTRIAL I/O PACK INTERFACE FEATURES
•
High density -
Single-size, industry-standard, IP module
footprint. Up to four units may be mounted on a 6U VMEbus
carrier board or five units may be mounted on a PCI carrier
board.
•
Local ID
- Each IP module has its own 8-bit ID information
which is accessed via data transfers in the "ID Read" space.
•
16-bit & 8-bit I/O
- Channel register Read/Write is
performed through D16 or D08 (EO) data transfer cycles in
the IP module I/O space.
•
High Speed
- Access times for all data transfer cycles are
described in terms of "wait" states. For the supplied IP
module example, wait states are utilized for all read and
write operations (see specifications for detailed information).
SIGNAL INTERFACE PRODUCTS
(See Appendix for more information on compatible products)
This IP module will mate directly to any industry standard IP
carrier board. A wide range of other Acromag IP modules and
carriers are also available to serve your signal conditioning and
interface needs.
The cables and termination panels, described in the following
paragraphs, represent some of the accessories available from
Acromag. Each Acromag carrier has its own unique accessories.
They are not all listed in this document. Consult your carrier
board documentation for the correct interface product part
numbers to ensure compatibility with your carrier board.
Cables:
Model 5025-551-X (Shielded Cable), or Model 5025-550-X
(Non-Shielded Cable): A Flat 50-pin cable with female
connectors at both ends for connecting AVME9630/9660, or
other compatible carrier boards, to Model 5025-552
termination panels. The unshielded cable is recommended
for digital I/O, while the shielded cable is recommended for
optimum performance with precision analog I/O applications.
Termination Panel:
Model 5025-552: A DIN-rail mountable panel that provides
50 screw terminals for universal field I/O termination.
Connects to all Acromag carriers (or other compatible carrier
boards) via flat 50-pin ribbon cable (Model 5025-550-X or
5025-551-X).
Transition Module:
Model TRANS-GP: This module repeats field I/O
connections of IP modules A through D for rear exit from a
VMEbus card cage. It is available for use in card cages
which provide rear exit for I/O connections via transition
modules (transition modules can only be used in card cages
specifically designed for them). It is a double-height (6U),
single-slot module with front panel hardware adhering to the
VMEbus mechanical dimensions, except for shorter printed
circuit board depth. It connects to Acromag Termination
Panel 5025-552 from the rear of the card cage, and to
AVME9630/9660 boards within the card cage, via flat 50-pin
ribbon cable (Model 5025-550-X or 5025-551-X).
IP1K110 FPGA ENGINEERING DESIGN KIT
Acromag provides an engineering design kit for the IP1K110
(sold separately), a “must buy” for first time IP1K110 module
purchasers. The design kit (model IP-1K110-EDK) provides the
user with the basic information required to develop a custom
FPGA program for download to the Altera FPGA. The design kit
includes a CD containing: schematics, parts list, part location
drawing, example VHDL source, example configuration file, and
other utility files. The IP1K110 is intended for users fluent in the
use of Altera MaxPlus II or Quartus II design tools.