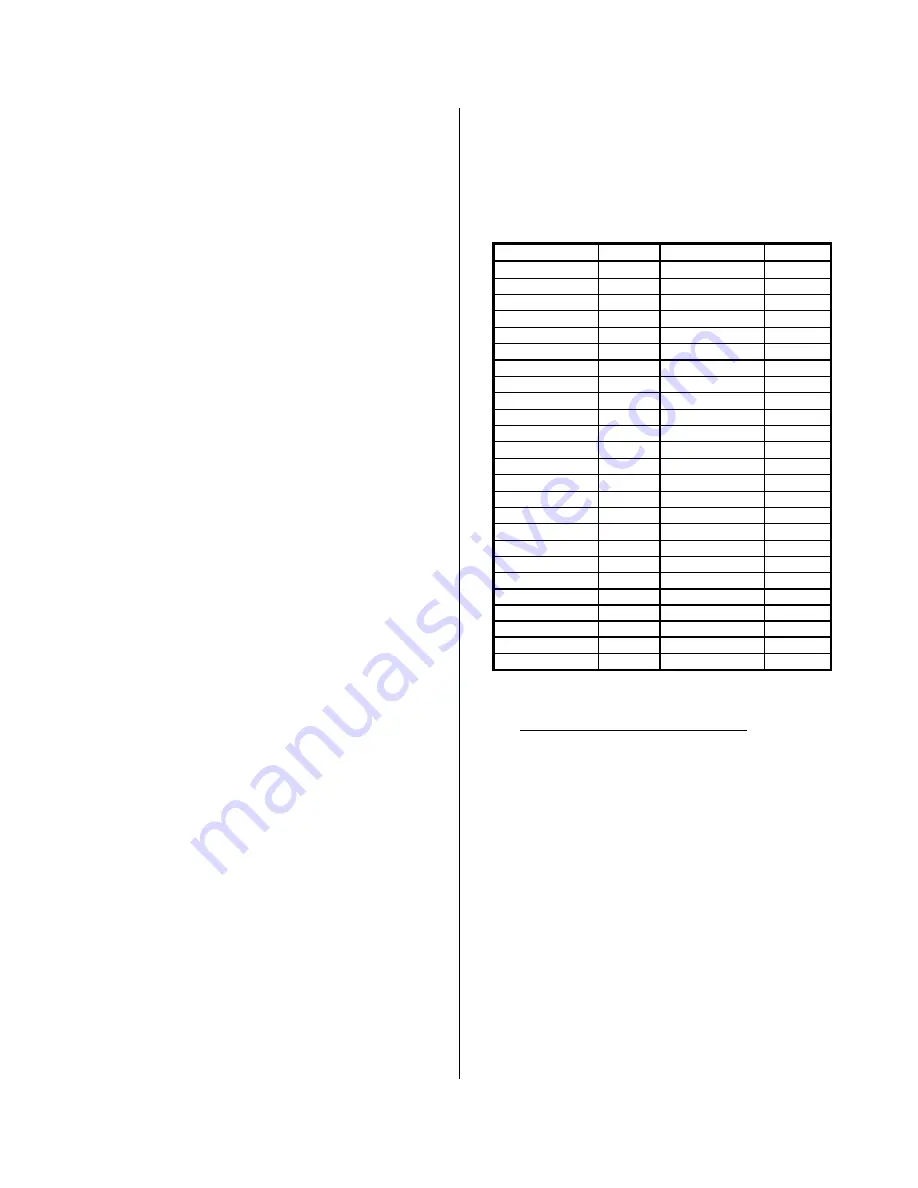
SERIES IP330 INDUSTRIAL I/O PACK 16-BIT HIGH DENSITY ANALOG INPUT MODULE
___________________________________________________________________________________________
- 6 -
Analog Inputs: Noise and Grounding Considerations
Differential inputs require two leads (+ and -) per channel, and
provide rejection of common mode voltages. This allows the
desired signal to be accurately measured. However, the signal
being measured cannot be floating--it must be referenced to
analog common on the IP module and be within the normal input
voltage range.
Differential inputs are the best choice when the input channels
are sourced from different locations having slightly different ground
references and when minimizing noise and maximizing accuracy
are key concerns. See Drawing 4501-591 for analog input
connections for differential and single-ended inputs. Shielded
cable of the shortest length possible is also strongly
recommended.
Single-ended inputs only require a single lead (+) per channel,
with a shared "sense" (reference) lead for all channels, and can be
used when a large number of input channels come from the same
location (e.g. printed circuit board). The channel density doubles
when using single-ended inputs, and this a powerful incentive for
their use. However, caution must be exercised since the single
"sense" lead references all channels to the same common which
will induce noise and offset to the degree they are different.
The IP330 is non-isolated, since there is electrical continuity
between the logic and field I/O grounds. As such, the field I/O
connections are not isolated from the carrier board and backplane.
Care should be taken in designing installations without isolation to
avoid noise pickup and ground loops caused by multiple ground
connections. This is particularly important for analog inputs when
a high level of accuracy/resolution is needed. Contact your
Acromag representative for information on our many isolated
signal conditioning products that could be used to interface to the
IP330 input module.
External Trigger Input/Output
The external trigger signal on pin 49 of the P2 connector can
be programmed to input a TTL compatible external trigger signal,
or output IP330 hardware generated triggers to allow
synchronization of multiple IP330s.
As an input, the external trigger must be a 5 Volt logic, TTL-
compatible, debounced signal referenced to analog common. The
external trigger signal is an active low edge sensitive signal. That
is, the external trigger signal will trigger the IP330 hardware on the
falling edge. Once the external trigger signal has been driven low,
it should remain low for a minimum of 500n seconds.
As an output an active-low TTL signal can be driven to
additional IP330s, thus providing a means to synchronize the
conversions of multiple IP330s. The additional IP330s must
program their external trigger for signal input and convert on
external trigger only mode. See section 3.0 for programming
details to make use of this signal.
IP Logic Interface Connector (P1)
P1 of the IP module provides the logic interface to the mating
connector on the carrier board. This connector is a 50-pin female
receptacle header (AMP 173279-3 or equivalent) which mates to
the male connector of the carrier board (AMP 173280-3 or
equivalent). This provides excellent connection integrity and
utilizes gold-plating in the mating area. Threaded metric M2
screws and spacers are supplied with the IP module to provide
additional stability for harsh environments (see Drawing 4501-434
for assembly details). Field and logic side connectors are keyed to
avoid incorrect assembly. The pin assignments of P1 are
standard for all IP modules according to the Industrial I/O Pack
Specification (see Table 2.4).
Table 2.4: Standard Logic Interface Connections (P1)
Pin
Description Number Pin
Description Number
GND 1 GND 26
CLK 2 +5V 27
Reset* 3 R/W* 28
D00 4
IDSEL*
29
D01 5
DMAReq0*
30
D02 6
MEMSEL*
31
D03 7
DMAReq1*
32
D04 8
IntSel*
33
D05 9
DMAck0*
34
D06 10
IOSEL*
35
D07 11
RESERVED
36
D08 12 A1 37
D09 13
DMAEnd*
38
D10 14 A2 39
D11 15
ERROR*
40
D12 16 A3 41
D13 17
INTReq0*
42
D14 18 A4 43
D15 19
INTReq1*
44
BS0* 20 A5 45
BS1*
21
STROBE*
46
-12V 22 A6 47
+12V 23 ACK* 48
+5V 24
RESERVED
49
GND 25 GND 50
An Asterisk (*) is used to indicate an active-low signal.
BOLD ITALIC
Logic Lines are NOT USED by this IP Model.
3.0 PROGRAMMING INFORMATION
IP IDENTIFICATION PROM - (Read Only, 32 Odd-Byte
Addresses)
Each IP module contains an identification (ID) information that
resides in the ID space per the IP module specification. This area
of memory contains 32 bytes of information at most. Both fixed
and variable information may be present within the ID space.
Fixed information includes the "IPAC" identifier, model number,
and manufacturer's identification codes. Variable information
includes unique information required for the module. The IP330 ID
information does not contain any variable (e.g. unique calibration)
information. ID space bytes are addressed using only the odd
addresses in a 64 byte block (on the “Big Endian” VMEbus). Even
addresses are used on the “Little Endian” PC ISA bus. The IP330
ID space contents are shown in Table 3.1. Note that the base-
address for the IP module ID space (see your carrier board
instructions) must be added to the addresses shown to properly
access the ID space. Execution of an ID space read requires 1
wait state.