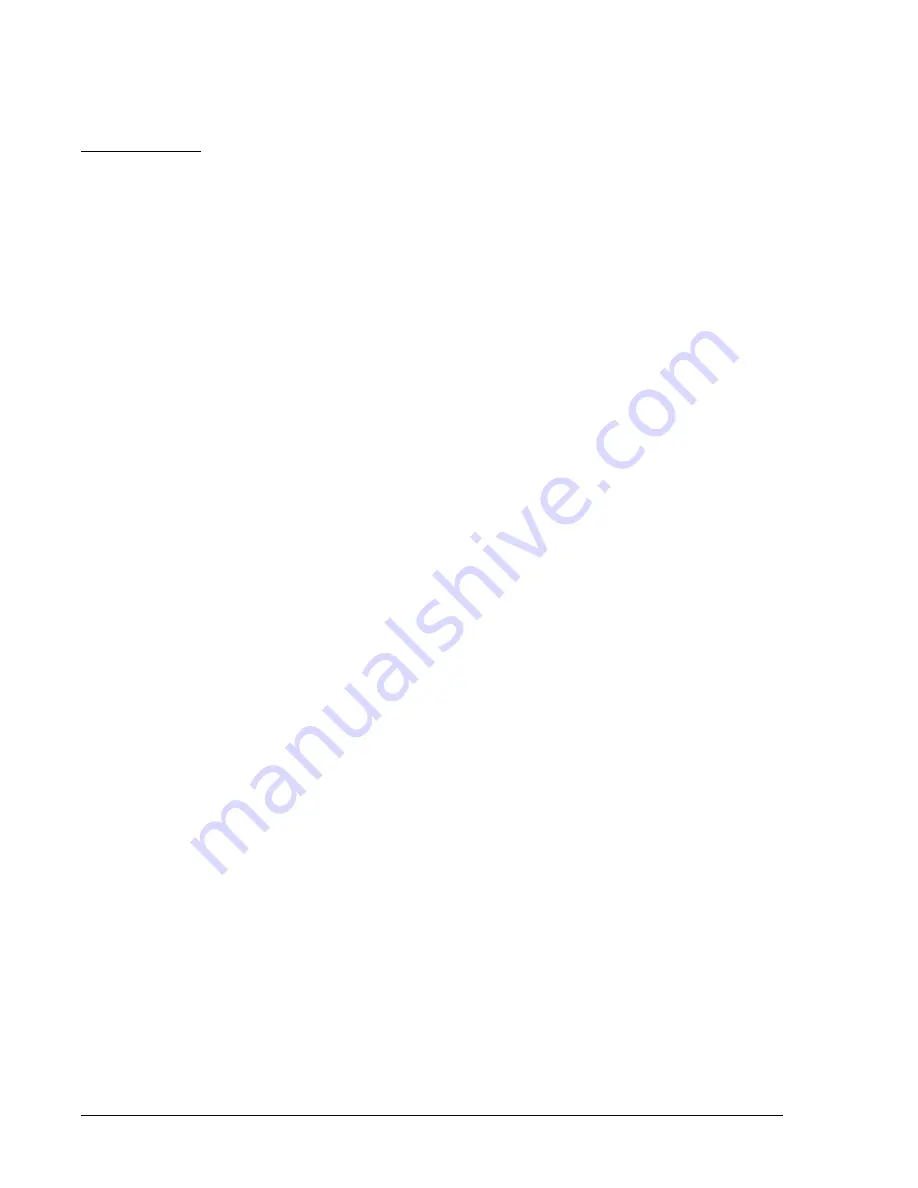
2-6
BE1-BPR Application
Another application is to prevent a BF operation due to stuck contacts on the BFI input. BFI input stuck
contacts would cause a false trip any time the fault detector picks up. This problem can be minimized by
using a control timer to limit the window of opportunity for which the input can cause a trip output.
Timer Diagnostics
In many applications it is desirable to have a record of the timing relationship between different events. In
order to acquire this record, data must be available and accumulated over a period of time. A method to
obtain and collect this data has been incorporated into the BE1-BPR relays. This method allows relative or
absolute timing between any input, output or internal operation (i.e. timers, fault detectors) to be logged into
a circular 40 event record. The data can be retrieved for analysis using the TLOG[n] command. In addition,
because some timing requirements are critical to proper system operation, an optional alarm output can be
automatically triggered if the time logged is outside a predetermined level. The logic used to save a timer
value to the log and the optional alarm time is programmable using the PTLOG[n] command.
Refer to
Section 1, General Information, Timing Diagnostics for detailed information on BF timing and an
example of using the timing diagnostics to create a MARGIN log.
Reclosing Timers
Each BE1-BPR relay provides six independent reclosing timers. Three reclosing timers (TD791, TD792, and
TD793) provide time delays for the multiple shots (one, two, and three). TD79R is the reset time delay,
TD79F is the reclose fail time delay, and TD79M is the maximum cycle timer.
Reclosing timer delay settings are programmable from the front panel or the serial port using the TD79
command. The three reclosing time delays can be set at zero or from 10 to 999 milliseconds in 1 millisecond
increments, 1 to 99 seconds in 0.1 second increments, or 100 to 600 seconds in 1 second increments. Each
of the reclosing timer may be disabled by a setting of zero. When a reclosing timer set at zero is reached
in the reclosing sequence, the reclosing sequence is interrupted and the relay will enter lockout.
Reset timer (TD79R) begins timing out when the RESET logic becomes TRUE (breaker closes). The reset
timer is reset when the breaker trips. If the reset timer times out while the breaker is closed, the recloser
goes to RESET.
If enabled, the reclose fail timer (TD79F) starts whenever a reclose output is given and stops when the
RESET logic indicates the breaker has closed. If the reclose fail timer times out before the RESET logic
becomes TRUE, the recloser sets the reclose fail diagnostic flag. The reclose fail diagnostic flag can be
inhibited by setting the time delay to zero. The reclose fail function can be inhibited by setting the reclosing
mode (TYPE) in the LR command to zero (0).
If the total reclosing time between reset states exceeds the maximum reclose cycle timer (TD79M) setting
(excluding time while in the WAIT state), the recloser goes to the lockout state. The maximum reclose cycle
timer can be inhibited by setting the time delay to zero.
Output Contacts
Each BE1-BPR relay has five isolated normally open (NO) output contacts (OUT1-OUT5) plus one isolated
normally closed (NC) alarm output (ALM). Output contact OUT1 is a high speed contact with a maximum
operating time of ¼ cycle. By using the PTARGET command, output relays can be programmed to latch
target data into memory.
Output contacts OUT1 through OUT5 are controlled by the status of the internal logic of signals O1 through
O5. If O[n] becomes TRUE, then the corresponding output relay is energized and closes the normally open
contacts. If the PHOLD feature is enabled, the output contacts are held in an energized state for 200 to 250
milliseconds when O[n] becomes true. Each output contact then resumes following the internal logic. The
PHOLD function ensures that the TRIP output doesn’t interrupt the trip coil current but allows the trip coil
current to be interrupted by the 52A contact.
Section 4, Functional Description provides more information
about the PHOLD command.
All output contacts are factory set to NO. However, OUT1 - OUT4 may be changed to NC by changing a
soldered jumper next to the output relays on the printed circuit board. NO contacts are typically used in trip
circuits and using this type of contact allows the relay electronics to be drawn out without activating the trip
Summary of Contents for BE1-BPR
Page 31: ...BE1 BPR Application 2 17...
Page 42: ...3 4 BE1 BPR Human Machine Interface Figure 3 4 BE1 BPR Relay Vertical Mount Front View...
Page 43: ...BE1 BPR Human Machine Interface 3 5 Figure 3 5 BE1 BPR Relay Vertical Mount Rear View...
Page 49: ...4 6 BE1 BPR Functional Description Figure 4 2 Enhanced BE1 BPR Menu Display Screens...
Page 50: ...BE1 BPR Functional Description 4 7 Figure 4 3 Standard BE1 BPR Menu Display Screens...
Page 94: ...5 4 BE1 BPR BESTlogic Figure 5 1 BESTlogic Function Blocks...
Page 121: ...BE1 BPR Installation 7 3 Figure 7 3 Overall Dimensions Vertical Mount...
Page 122: ...7 4 BE1 BPR Installation Figure 7 4 Overall Dimensions Side View Vertical Mount...
Page 123: ...BE1 BPR Installation 7 5 Figure 7 5 Panel Drilling Diagram Vertical Mount...