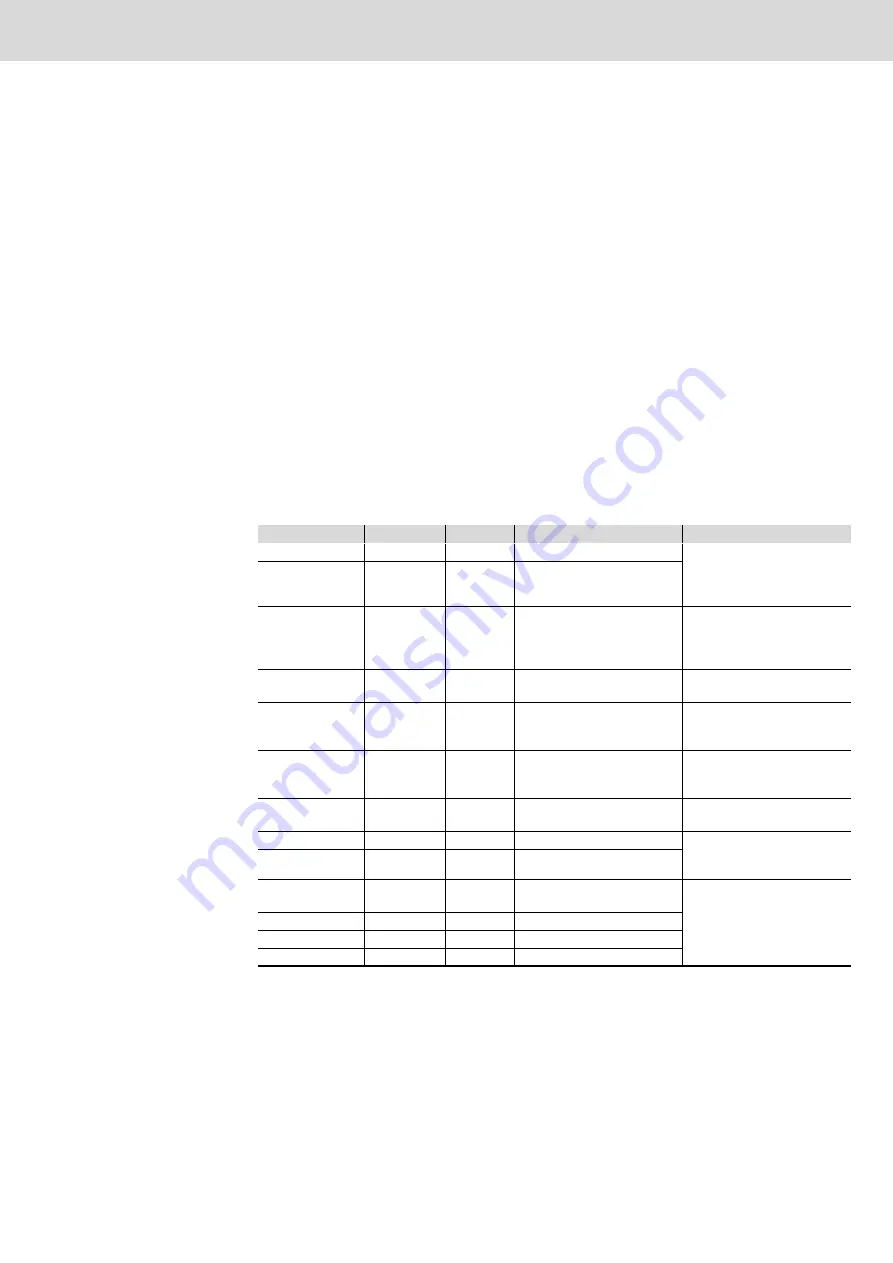
3 608 878 300
Tightening Technology |
Bosch Rexroth AG 497
System 350
| 3 608 878 300/2019-03
is set. Also an error code may be set in the ErrorCode output byte (valid in case of rising edge of
ReportNOK). Acceptance of the result is acknowledged by the PLC by disabling StartReport. In this
case, the tightening controller reacts by removal AckReportStart and clearing of the signals
ReportOK, ReportNOK and ErrorCode.
•
ID code (ID-Number and ASCII-String): Here, the ID codes for the component to be processed are
set by the PLC. The ID codes are applied with rising edge of InPos and saved internally. Additionally,
the ID codes are transferred to the involved applications (or the tightening channels).
•
FOx_PosNo: The position number is internally used for generation of the application and channel IDs.
The position number must be applied 200ms before the actual start of the application (via FO_CW/
FO_CCW).
•
Type_No: The type number is used internally to establish the list of assignment between tightening
channels, programs and PLUS-QIs in the tightening system configuration. In case of rising edge of
InPos, the Type_No has to be applied and is then internally checked and generated after checking
of signals AckInPos or AckTypOk.
•
ChnErrAck: A new channel system error was applied by the PLC (see below, signals Ch_ErrCode/
Ch_ChnNum/Ch_ErrClass). This is the acknowledgement for the ChnErr signal. With rising edge of
ChnErr, the tightening controller indicates that a new channel system error is available for
acceptance by the PLC. The error is read and ChnErrAck is set by the PLC. Afterwards, acceptance
is recognized and marked internally by the tightening controller and the signal ChnErr is reset. This
must also be acknowledged by the PLC by disabling of ChnErrAck. Both participants are now ready
for new transmission of system errors.
Additional general instructions:
•
If data is not to be transmitted to PLUS for specific tightening processes, internal data processing
can be prevented by setting the
FOx_DisRp
signal
•
The position information is always evaluated. For applications without positioning, a fixed position
number must be transmitted and also configured in BS350 (typically 0).
Table 6–180:
Outputs
Signal
Data type
Address
Signal name/description
Validity/notes
ReportOK
Bool
%0.5
Report OK
One of the two signals is set to
indicate to the PLC the end of
the PLUS transmission started
by StartReport.
ReportNOK
Bool
%0.6
Report NOK
AckReportStart
Bool
%0.7
Acknowledge start report
The signal is set as
acknowledgement of
StartReport (and reset after
reset of StartReport).
AckInPos
Bool
%1.0
Acknowledge in position
Acknowledgement for InPos of
the PLC (see above)
AckTypOk
Bool
%1.1
Acknowledge for TypeNo OK
Acknowledgement that
Type_No of the PLC was
correctly applied (see above).
ChnErr
Bool
%1.2
New channel error active
Rising edge indicates validity of
channel system errors (see
above)
ErrorCode
Byte
%56
Error code for AckReportStart
Error code if ReportNOK was
set.
KE_ErrCode
Word
%57
Error code of KE system error
Set as long as a system error is
active. If no KE system error,
KE_ErrCode = 0.
KE_ErrClass
Byte
%59
Error class of KE system error
Ch_ChnNum
Byte
%60
Applicable channel number for
the following two fields
Valid with rising edge of ChnErr
Ch_ErrCode
Word
%61
Channel system error code
Ch_ErrClass
Byte
%63
Channel system error class
KE_ErrCode
Word
%57
Error code of KE system error
Summary of Contents for Rexroth Tightening System 350
Page 4: ...4 641 Bosch Rexroth AG Schraubtechnik System 350 3 608 878 300 2019 03 ...
Page 120: ...120 641 Bosch Rexroth AG Tightening Technology 3 608 878 300 System 350 3 608 878 300 2019 03 ...
Page 194: ...194 641 Bosch Rexroth AG Tightening Technology 3 608 878 300 System 350 3 608 878 300 2019 03 ...
Page 638: ...638 641 Bosch Rexroth AG Tightening Technology 3 608 878 300 System 350 3 608 878 300 2019 03 ...